Flow Valve
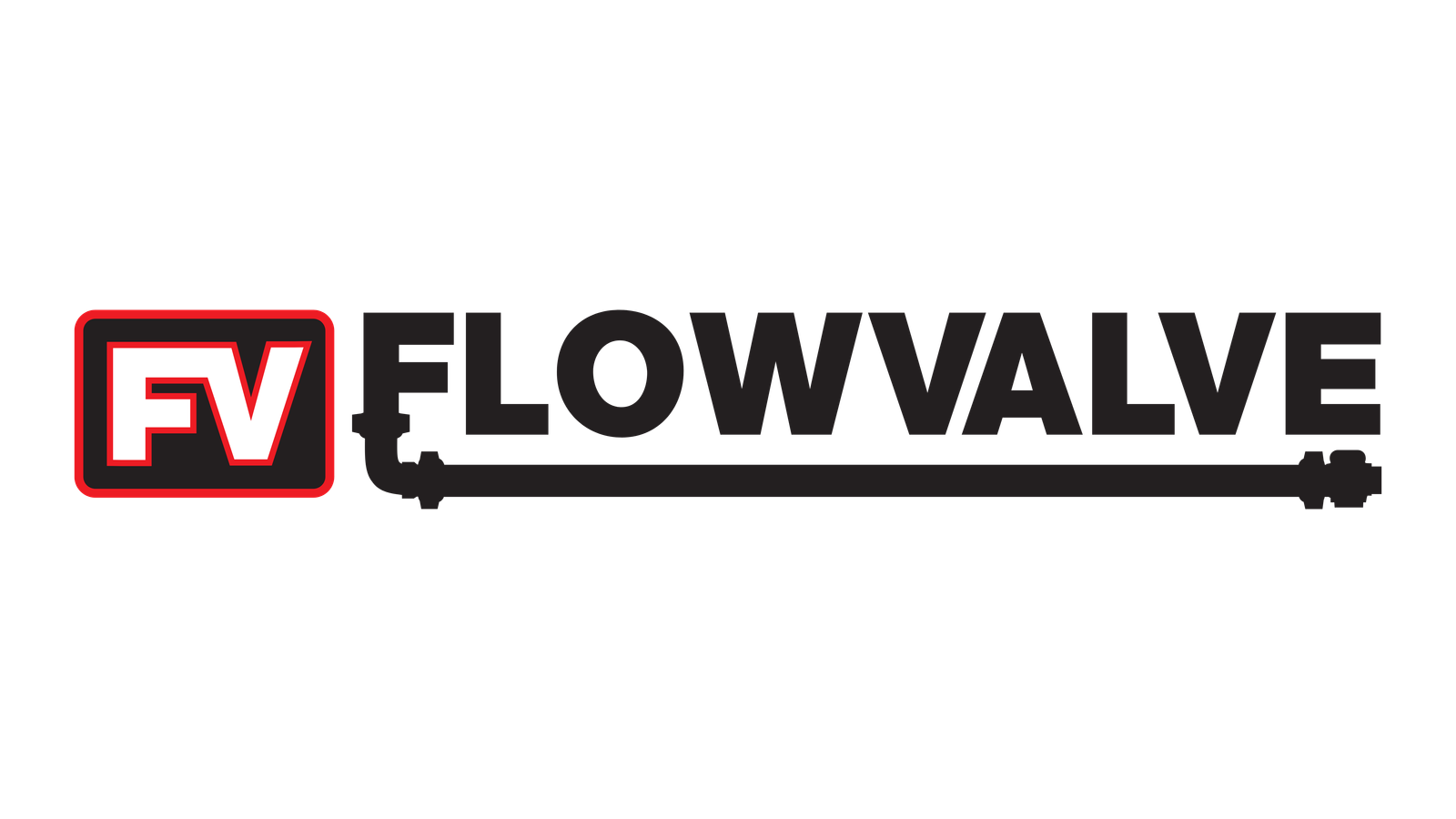
- Introduction
- Check Valve
- Flowline
- Hose loops
- Integral fittings
- Plug catcher
- Plug valve
- Plug valve super seal
- Swivels
Introduction
Over 230,000 sq. ft. of manufacturing space under one roof-our facility offers unmatched machining, fabricating and assembling capabilities. Our organization boasts over 255 machines, which gives us the ability to rapidly respond to customer demand. Our machine arsenal includes live tooling lathes, 5-axis boring mills, vertical machining centers and horizontal machining centers. FlowValve and KERR Pumps are one of the largest machining companies in all of Oklahoma.
FlowValve meets and exceeds the requirements stated
in the ISO :001:2015 quality manual. We believe in not only meeting, but exceed mg our customers’ needs through continuous improvement. All of our products meet or exceed API standards. Our commitment for perfection is the gold standard for well service products. Every FlowValve part is hydro-tested at 1 ½ times CWP. During the testing each part is inspected with a high focus camera lens to check for leaks. Once each part passes the test, results are charted and stored in our database by serial number.
Our PQC with iPAR technology is a revolutionary quality system
that uses a touch trigger probe to inspect every part in the machine
as it is made. It detect deviations of the machine and automatically recalibrates itself during the machining process.
TRANSFER THE WEAR
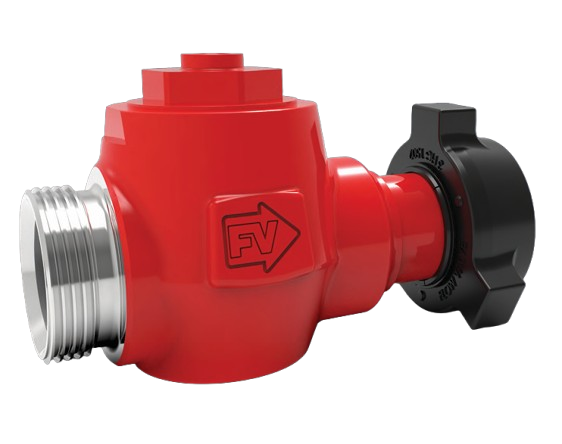
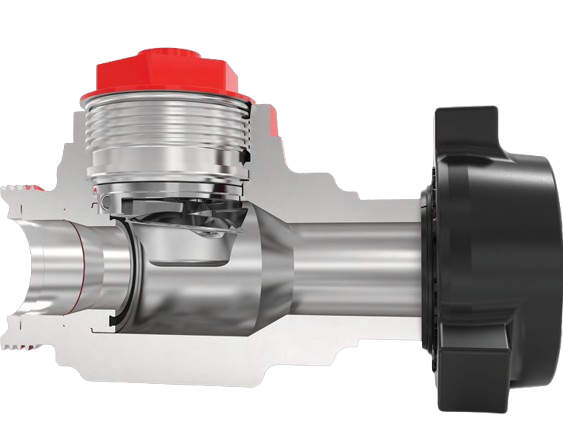
Our revolutionary patent-pending Super Seal™ check valve is designed to transfer the wear from the normal failure points. We have re-engineered the flapper, seat, pin, and halo to perform at a whole new level. Now, for the first time ever, there is a check valve designed to hold up to today’s frac jobs!
HYDRO-DYNAMIC
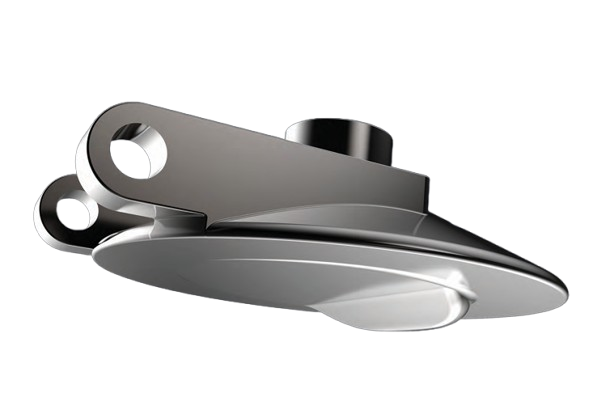
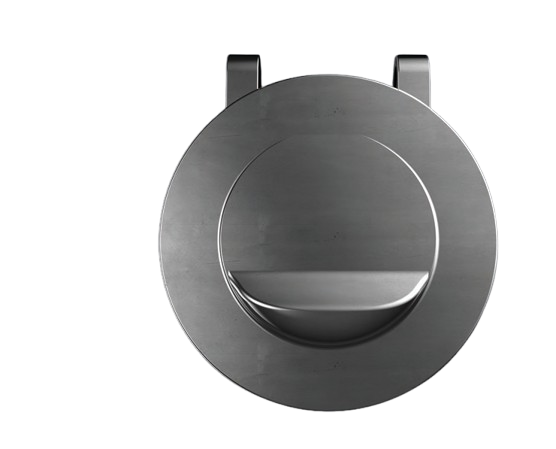
Our patent-pending flapper design has a unique geometry that Transfers the Wear away from the sealing surfaces of the flapper. This hydro-dynamic feature provides extra liftoff for the flapper, redirecting the flow down to the through bore without having direct contact with the sealing surfaces of the flapper!
WHERE’S THE COATING?
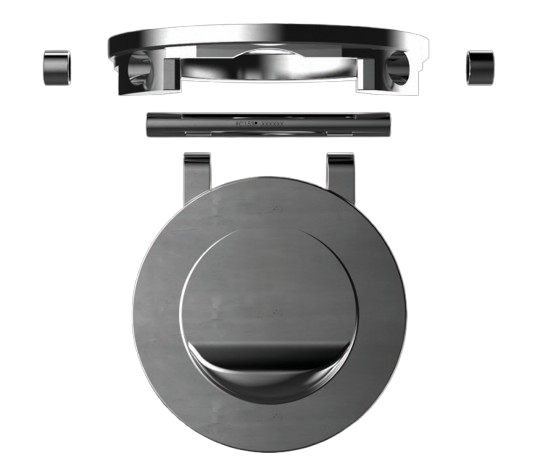
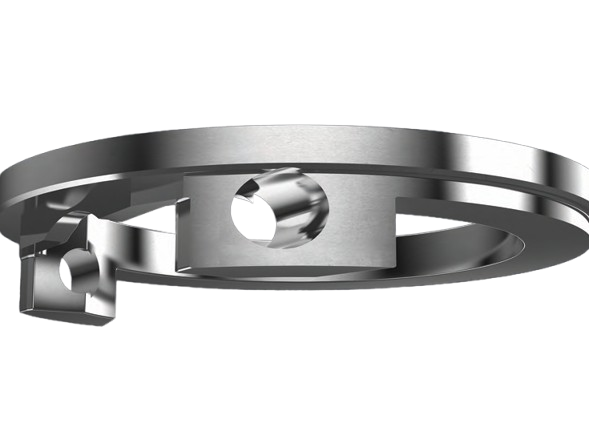
We designed the Check Valve SS™ flapper to last well beyond 40 stages! Our proprietary coating is 10X more wear and erosion resistant than standard polyurethane. Frequent flapper kit changes are now a thing of the past.
ENGINEERED BUSHING SYSTEM
In standard bushing systems, as the pin and halo wear, the flapper begins to drop, causing an inadequate seal. Our Super Seal Check Valve™ HALO is engineered with a patent-pending, tungsten carbide bushing system that virtually eliminates the wear from the rotating pin. This new design feature prevents the flapper from dropping, maintaining a proper seal. Our advanced bushing system gives the degree of freedom necessary for sealing performance, while extending the life of the product!
HELLO HALO
Our new HALO is designed with the Equipment Operator in mind. Simply drop in the flapper assembly and remove the HALO by hand. This design means no more press fit that’s hard to get in and out. Field maintenance just got a whole lot easier.
SUPER SEAL DESIGN
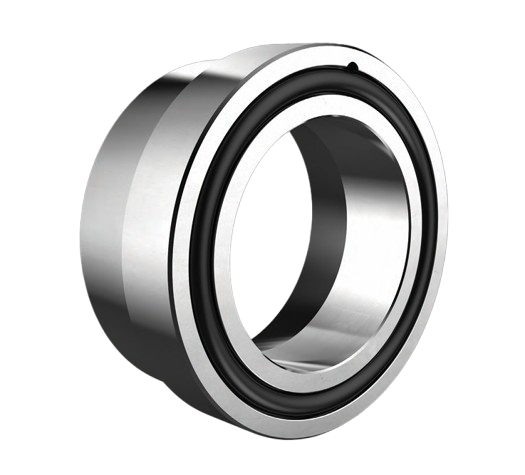
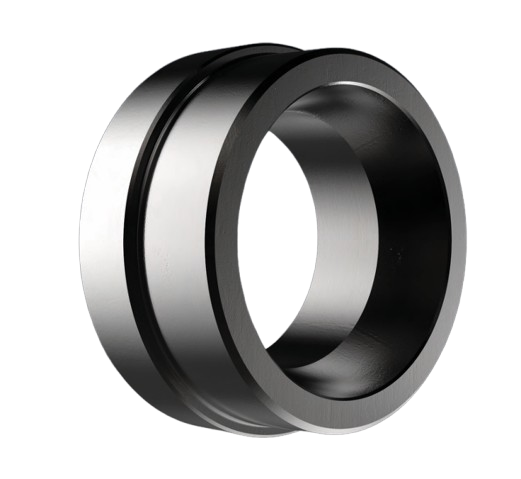
Seal placement is critical. That’s why we designed our seal to snap into the face of the seat, and out of the direct flow path. This design decision allowed us to focus more on sealing instead of worrying about a coating that can hold up to abrasive proppants. Our Check Valve SS™ sealing technology is engineered for high pressure sealing
A SEAT YOU’RE FAMILIAR WITH
Standard Check Valve seats are hard to maintenance. Some are press fit in and a nightmare to remove. Others are threaded and prove difficult to get out. We designed our seat to taper lock in place. This is the same technology used to seal and lock fluid end valve seats! Each check valve seat is made with a proprietary stainless steel, then heat treated for extreme erosion
and corrosion resistance.
TRANSFER THE WEAR
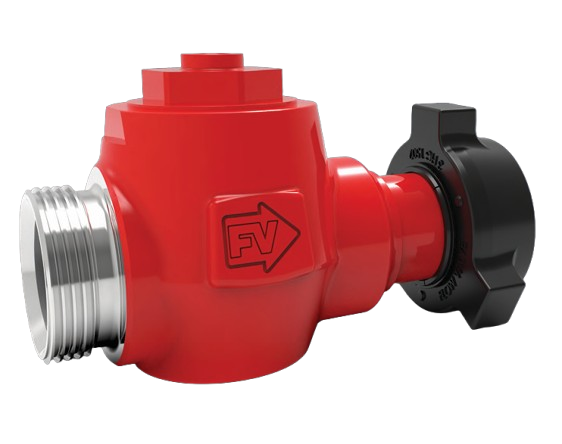
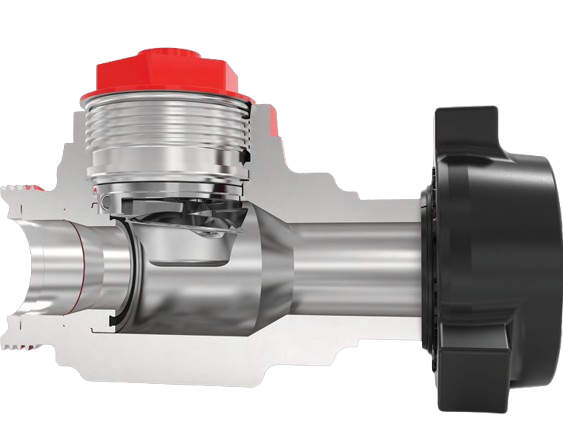
Our revolutionary patent-pending Super Seal™ check valve is designed to transfer the wear from the normal failure points. We have re-engineered the flapper, seat, pin, and halo to perform at a whole new
level. Now, for the first time ever, there is a check valve designed to hold up to today’s frac jobs!
HYDRO-DYNAMIC
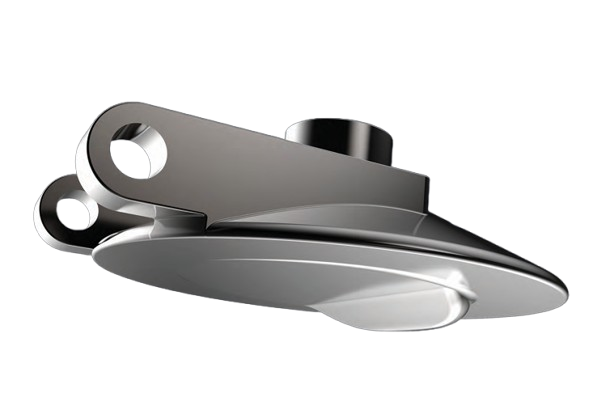
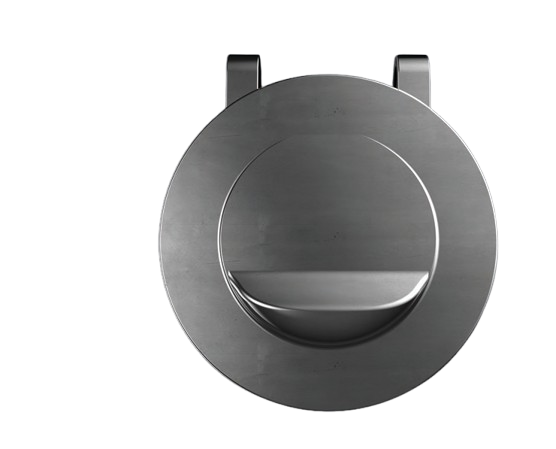
Our patent-pending flapper design has a unique geometry that Transfers the Wear away from the sealing surfaces of the flapper. This hydro-dynamic feature provides extra liftoff for the flapper, redirecting the flow down to the through bore without having
direct contact with the sealing surfaces of the flapper!
WHERE’S THE COATING?
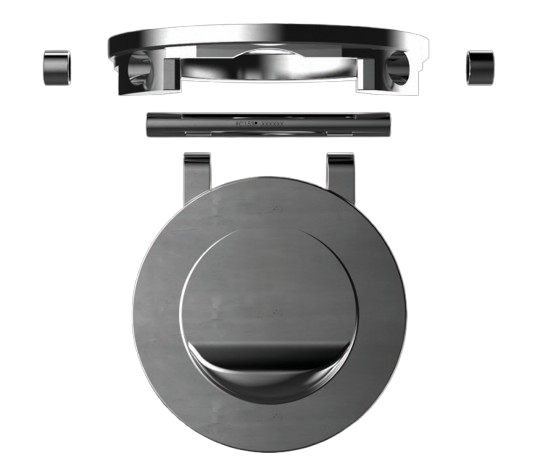
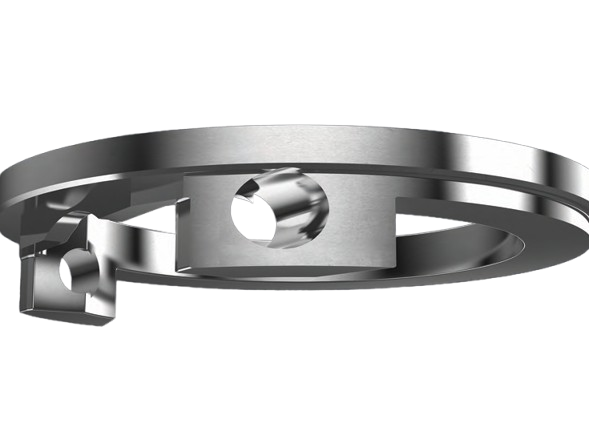
We designed the Check Valve SS™ flapper to last well beyond 40 stages! Our proprietary coating is 10X more wear and erosion resistant than standard polyurethane. Frequent flapper kit changes are now a thing of the past.
ENGINEERED BUSHING SYSTEM
In standard bushing systems, as the pin and halo wear, the flapper begins to drop, causing an inadequate seal. Our Super Seal Check Valve™ HALO is engineered with a patent-pending, tungsten carbide bushing system that virtually eliminates the wear from the rotating pin. This new design feature prevents the flapper from dropping, maintaining a proper seal. Our advanced bushing system gives the degree of freedom necessary for sealing performance, while extending the life of the product!
HELLO HALO
Our new HALO is designed with the Equipment Operator in mind. Simply drop in the flapper assembly and remove the HALO by hand. This design means no more press fit that’s hard to get in and out. Field maintenance just got a whole lot easier.
SUPER SEAL DESIGN
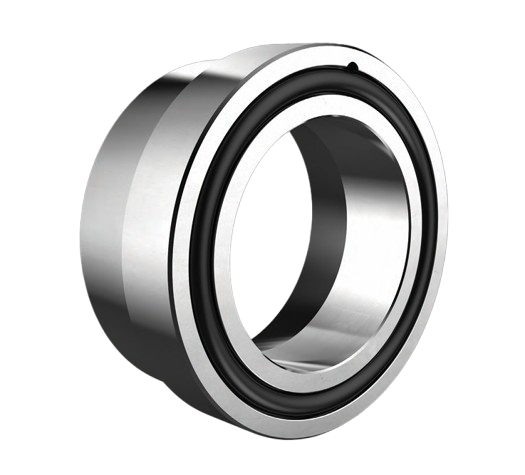
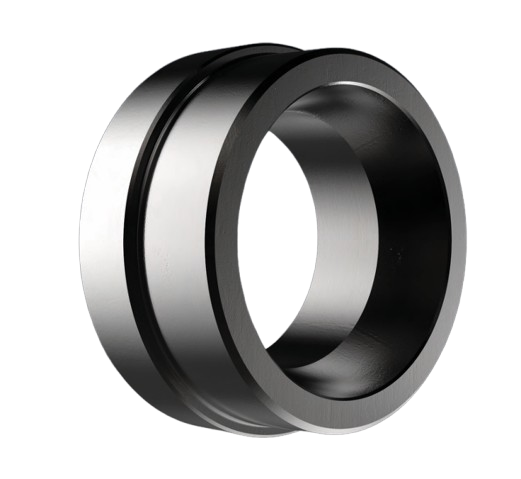
Seal placement is critical. That’s why we designed our seal to snap into the face of the seat, and out of the direct flow path. This design decision allowed us to focus more on sealing instead of worrying about a coating that can hold up to abrasive proppants. Our Check Valve SS™ sealing technology is engineered for high pressure sealing
A SEAT YOU’RE FAMILIAR WITH
Standard Check Valve seats are hard to maintenance. Some are press fit in and a nightmare to remove. Others are threaded and prove difficult to get out. We designed our seat to taper lock in place. This is the same technology used to seal and lock fluid end valve seats! Each check valve seat is made with a proprietary stainless steel, then heat treated for extreme erosion
and corrosion resistance.
Seamless integration
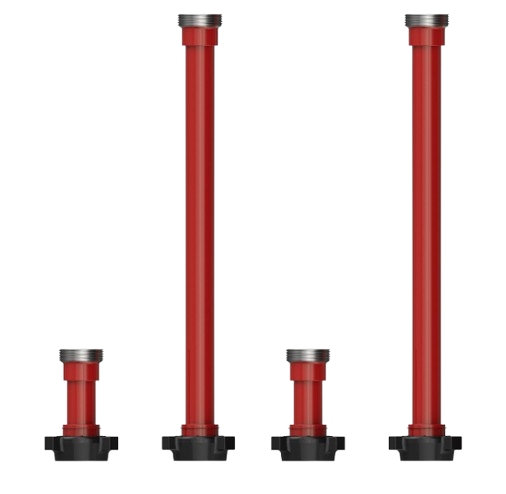
The design of the NPST pup joint takes end connections and attaches them to threaded pipe. The quality of these parts is critical to form and function. Our process is designed for a seamless integration between pipe and union. It’s hard to tell where one part begins and the other ends
Custom lengths in every size
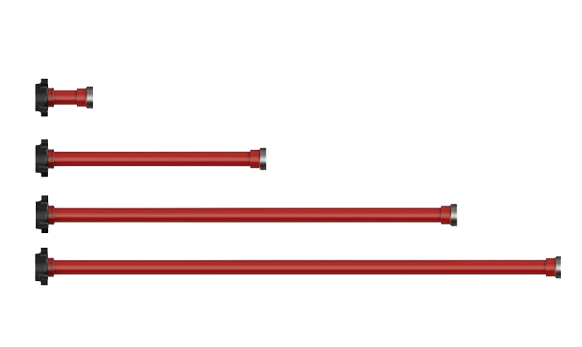
Our standard pup joints come in a variety of lengths from one foot to twenty feet. We also make custom lengths everywhere in between. At FLOWVALVE, we are certain that getting the perfect fit is easy with size configurations offered in 2”, 3”, 4” Fig 1502 and 4” Fig 1002.
Flowline that flows
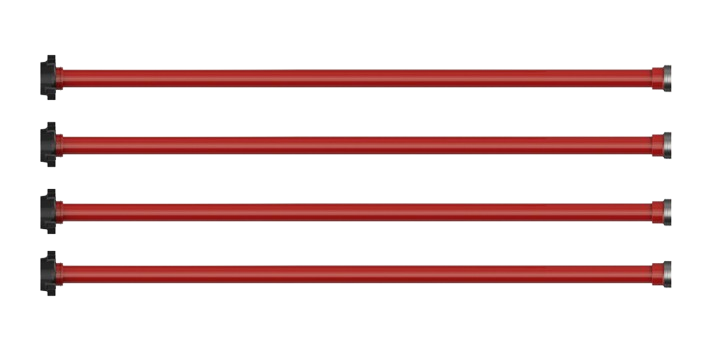
Saying our NPST pup joint production process is efficient is an understatement. From saw cutting to shipping, our industrial
engineers mapped the most streamlined production processes. We reviewed every detail and designed a system that makes FLOWVALVE’s flowline flow.
Seamless integration
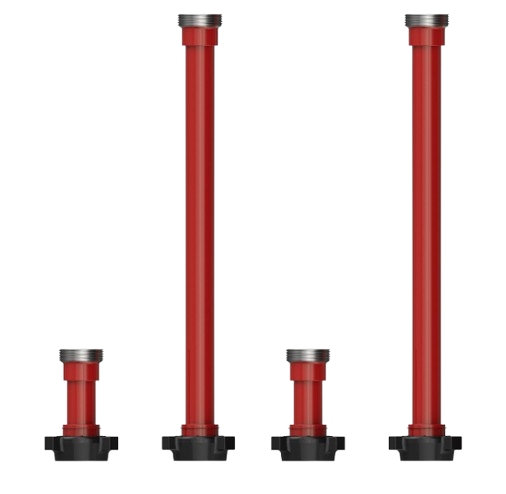
The design of the NPST pup joint takes end connections and attaches them to threaded pipe. The quality of these parts is critical to form and function. Our process is designed for a seamless integration between pipe and union. It’s hard to tell where one part begins and the other ends
Custom lengths in every size
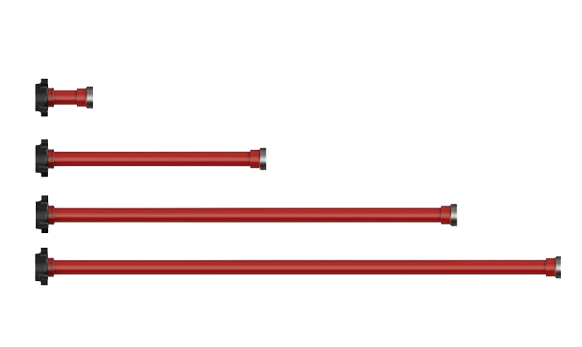
Our standard pup joints come in a variety of lengths from one foot to twenty feet. We also make custom lengths everywhere in between. At FLOWVALVE, we are certain that getting the perfect fit is easy with size configurations offered in 2”, 3”, 4” Fig 1502 and 4” Fig 1002.
Flowline that flows
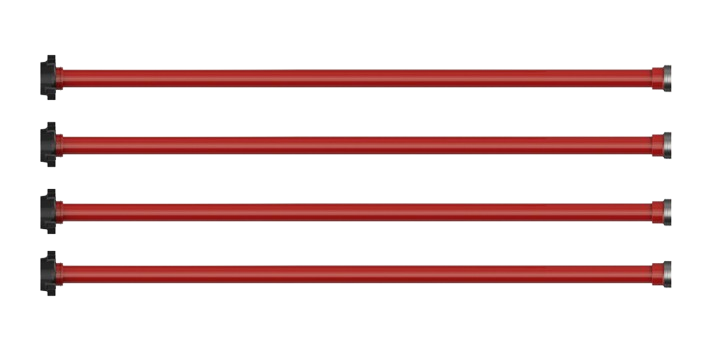
Saying our NPST pup joint production process is efficient is an understatement. From saw cutting to shipping, our industrial
engineers mapped the most streamlined production processes. We reviewed every detail and designed a system that makes FLOWVALVE’s flowline flow.
Endless possibilities
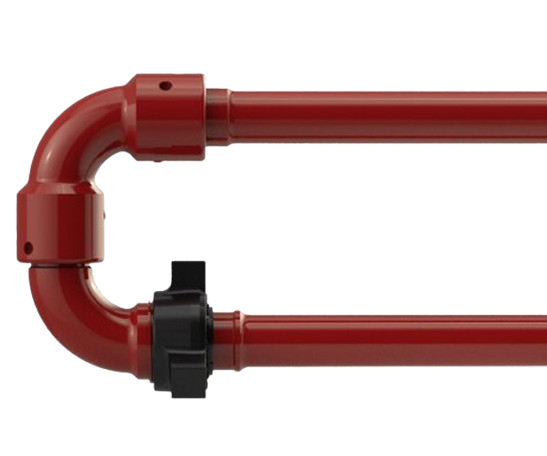
FLOWVALVE hose loops are used in a wide variety of well service applications, such as circulating lines, water lines, discharge lines, well test lines and temporary flowlines. Our hose loops are used most extensively for primary and secondary cementing operations.
A variety of options
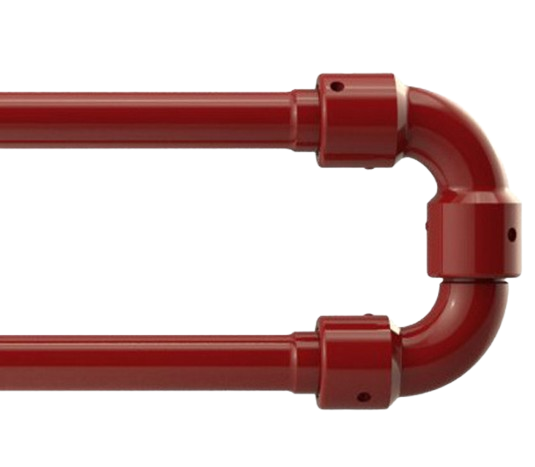
Different jobs require different solutions, and that is why we offer our hose loops in 6’, 8’, 10’ and 12’ lengths. This variety of lengths gives you the opportunity to choose the right products for your job.
Forefront of technology

By implementing an innovative and unique swivel joint technology, FLOWVALVE hose loops can easily move in any lateral direction. The swivel joint used in our hose loops is also used to control vibration and absorb shock. Once you used our hose loops, you will want to use them forever.
More life equals more value
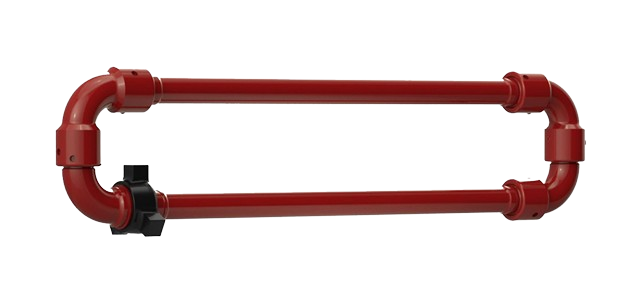
FLOW VALVE hose loops are made from high alloy U.S. steel. Our new advanced material results in better heat treatment and more durable products. With this new material, we have been able to extend the life of our hose loops even further.
Tell us why
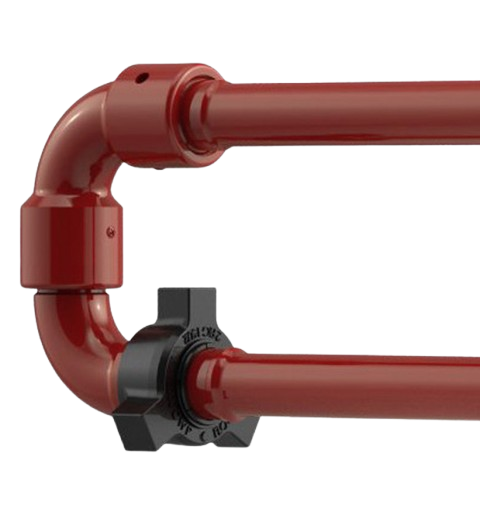
Why buy hose loops that have undergone a thorough design analysis review? Why use a product that has been tested at 1½ CWP? Why rely on a product that simply lasts longer in the field? Here at FLOWVALVE, we ask, “Why not?”
Endless possibilities
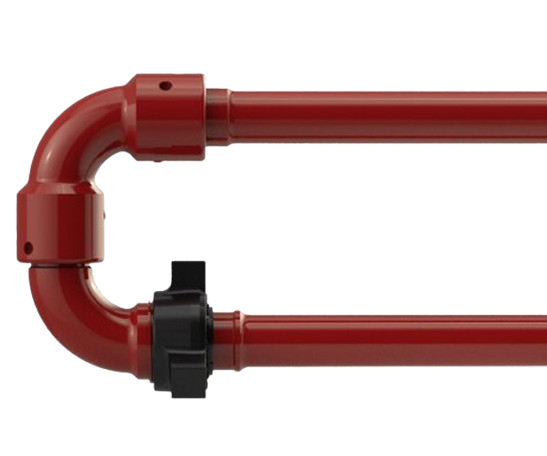
FLOWVALVE hose loops are used in a wide variety of well service applications, such as circulating lines, water lines, discharge lines, well test lines and temporary flowlines. Our hose loops are used most extensively for primary and secondary cementing operations.
A variety of options
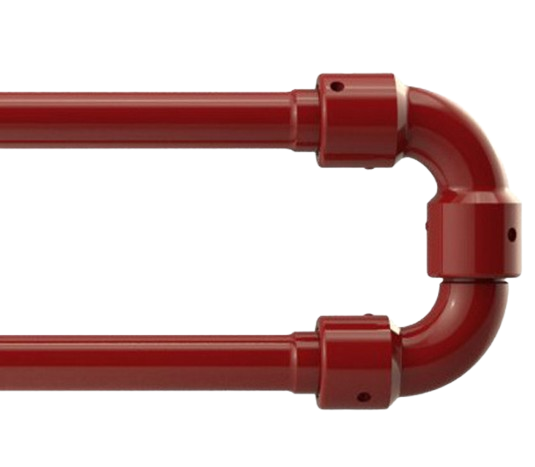
Different jobs require different solutions, and that is why we offer our hose loops in 6’, 8’, 10’ and 12’ lengths. This variety of lengths gives you the opportunity to choose the right products for your job.
Forefront of technology

By implementing an innovative and unique swivel joint technology, FLOWVALVE hose loops can easily move in any lateral direction. The swivel joint used in our hose loops is also used to control vibration and absorb shock. Once you used our hose loops, you will want to use them forever.
More life equals more value
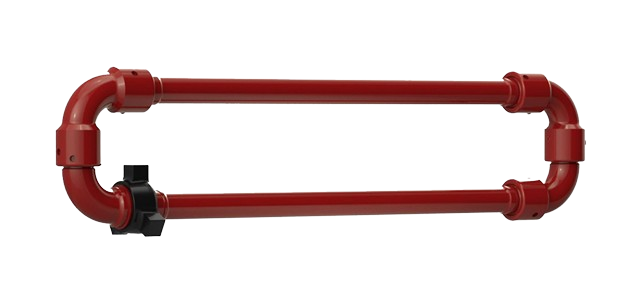
FLOW VALVE hose loops are made from high alloy U.S. steel. Our new advanced material results in better heat treatment and more durable products. With this new material, we have been able to extend the life of our hose loops even further.
Tell us why
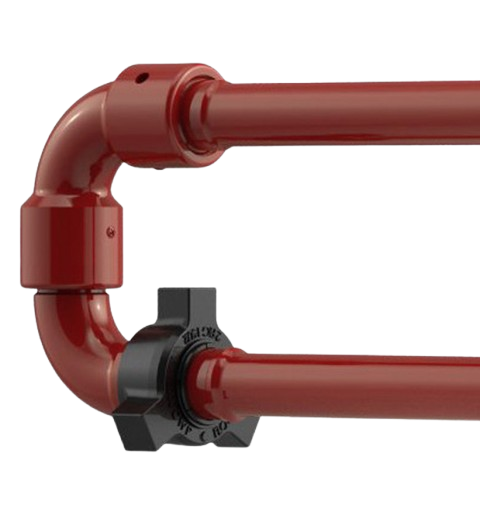
Why buy hose loops that have undergone a thorough design analysis review? Why use a product that has been tested at 1½ CWP? Why rely on a product that simply lasts longer in the field? Here at FLOWVALVE, we ask, “Why not?”
Tees
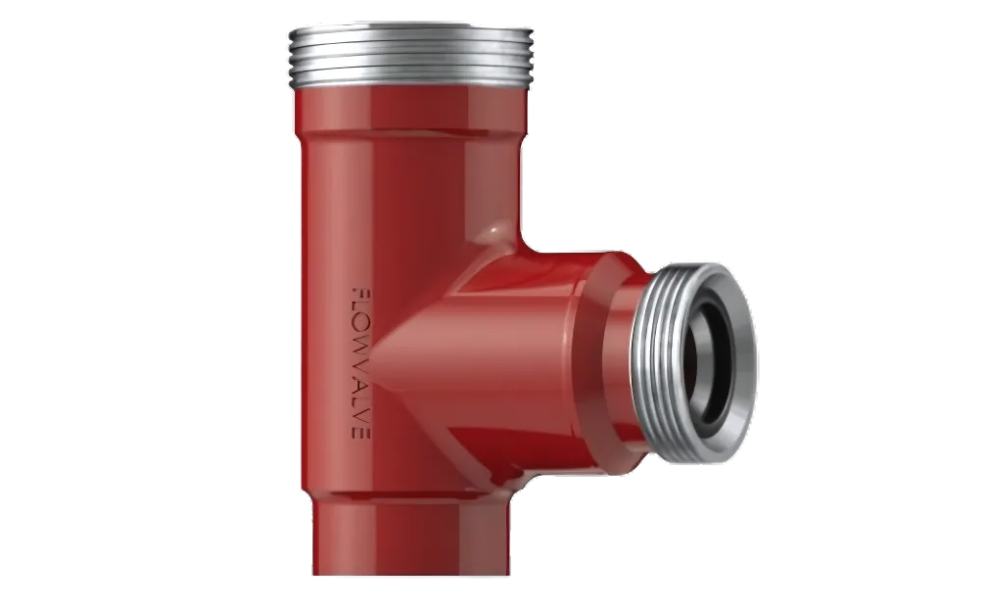
FLOWVALVE tees are widely used in hard plumbing applications. Our tees have an amazing repeatability for overall part length. This reliability makes it easy to hard plumb your red iron. With multiple configurations and sizes, our tees are the best way to wing up.
Crosses
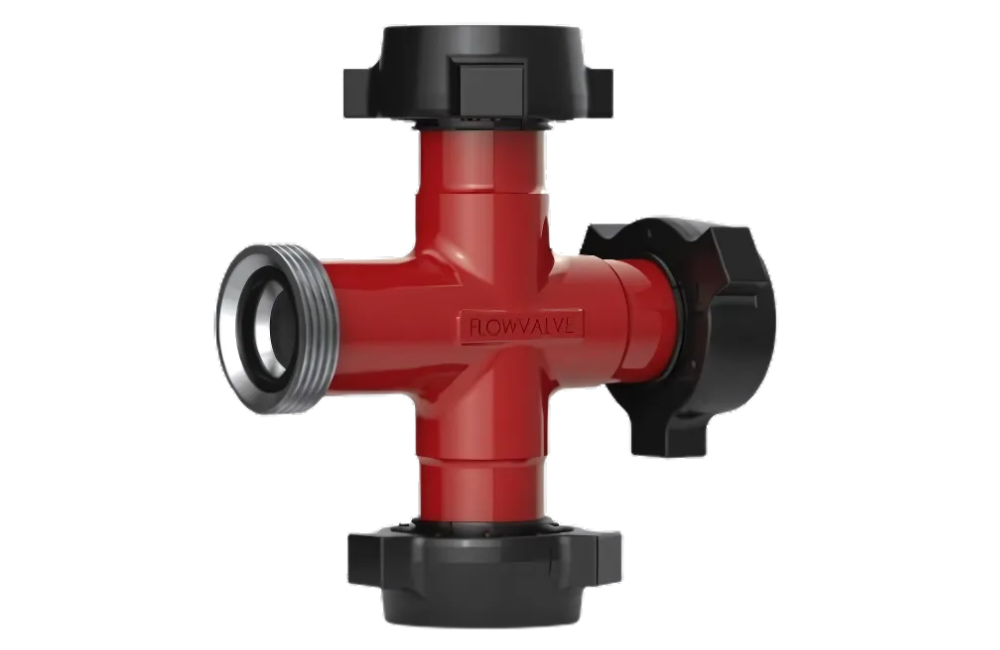
A cross between precision and performance. With precision hammer unions and the best sealing technology available, our crosses are great for applications where an intersecting flow is needed. Each cross is machined from high alloy forged steel that is heat treated for long lasting performance.
Cushion ells
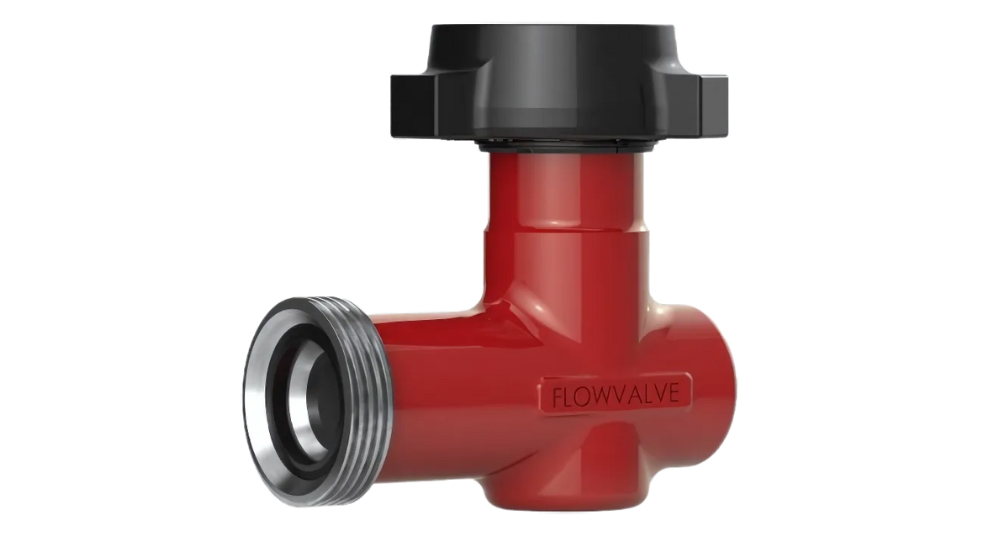
Cushion from the male or female. With extra material at the end of the elbow, our cushion ells are designed for extended service life. This feature behaves as a shock absorber, helping combat wear from abrasive slurry used in high pressure pumping.
Sweep 90’s
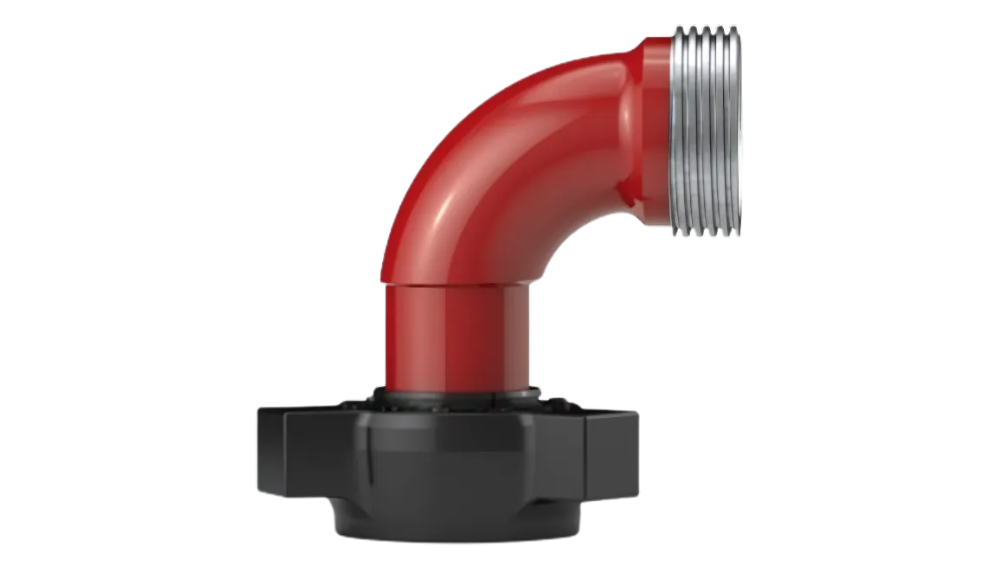
Bent 90 degrees for a smoother flow. With our swivel bending technology, we are able to bend a 90 degree elbow that can be used as an additional option for flowing 90 degrees. Because
of their low wear rate and smoother flow, sweep 90’s are a very popular choice for flowback operations.
Crossovers
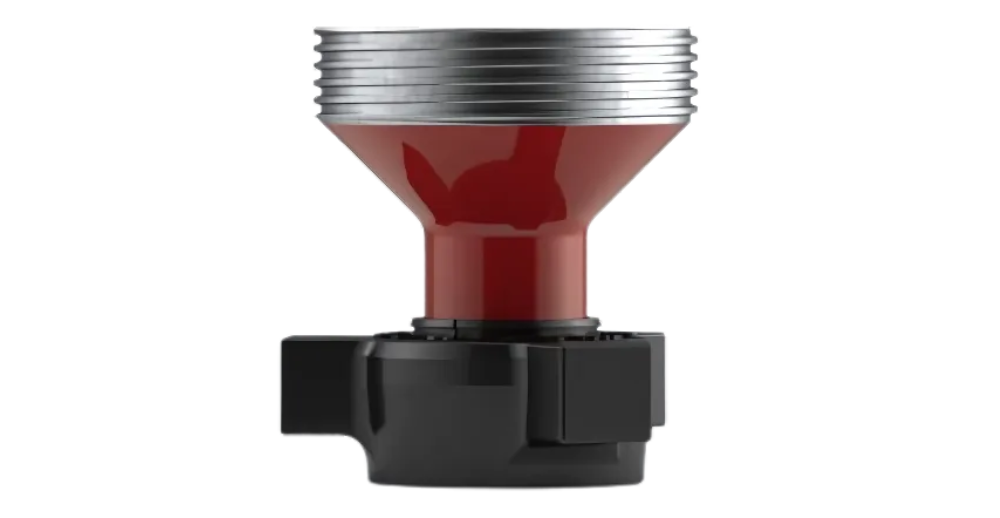
Change over from one size to another. We offer every combination of cross overs in 1”, 1 ½”, 2”, 3” and 4” Fig 1502 and 4” Fig 1002 connections. We carry an assortment of crossovers in stock and can make to order with our state of the art machining cells. We also machine special length crossovers on request.
Laterals
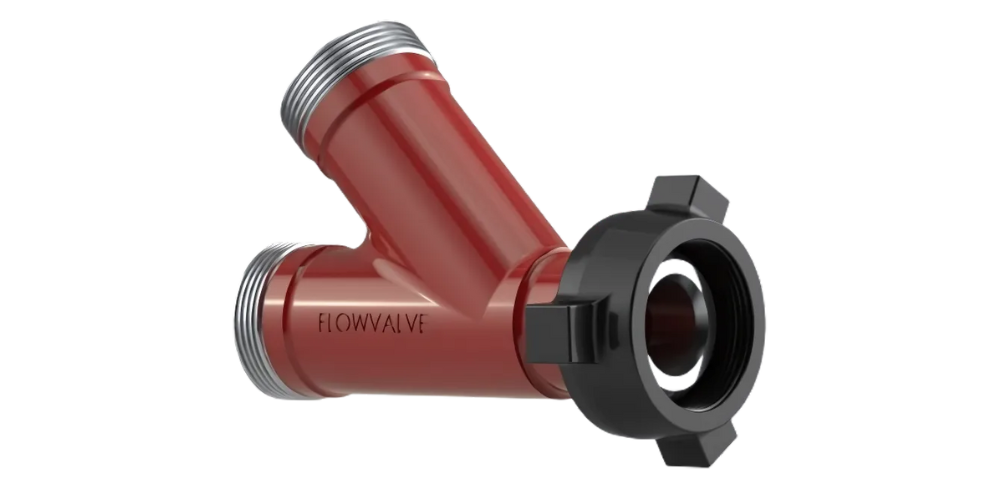
A great way to branch out. Our laterals are frequently used in frac manifolds and other high pressure manifolds. Each lateral is machined from U.S. forged, heat treated steel. They are available in 3” Fig 1502, 4” Fig 1502 and 4” Fig 1002 working pressures with custom end connections to fit your needs.
Tees
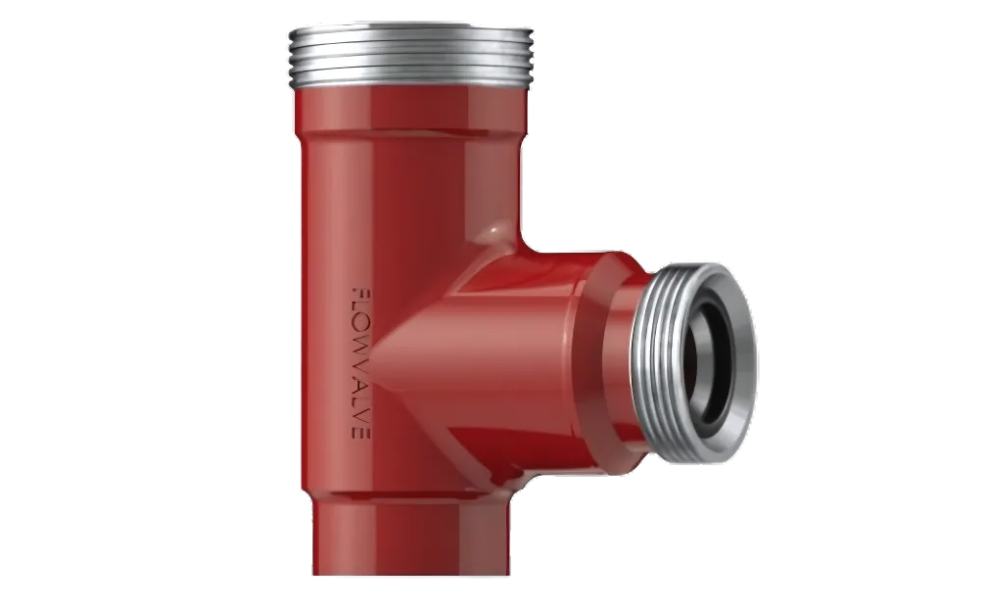
FLOWVALVE tees are widely used in hard plumbing applications. Our tees have an amazing repeatability for overall part length. This reliability makes it easy to hard plumb your red iron. With multiple configurations and sizes, our tees are the best way to wing up.
Crosses
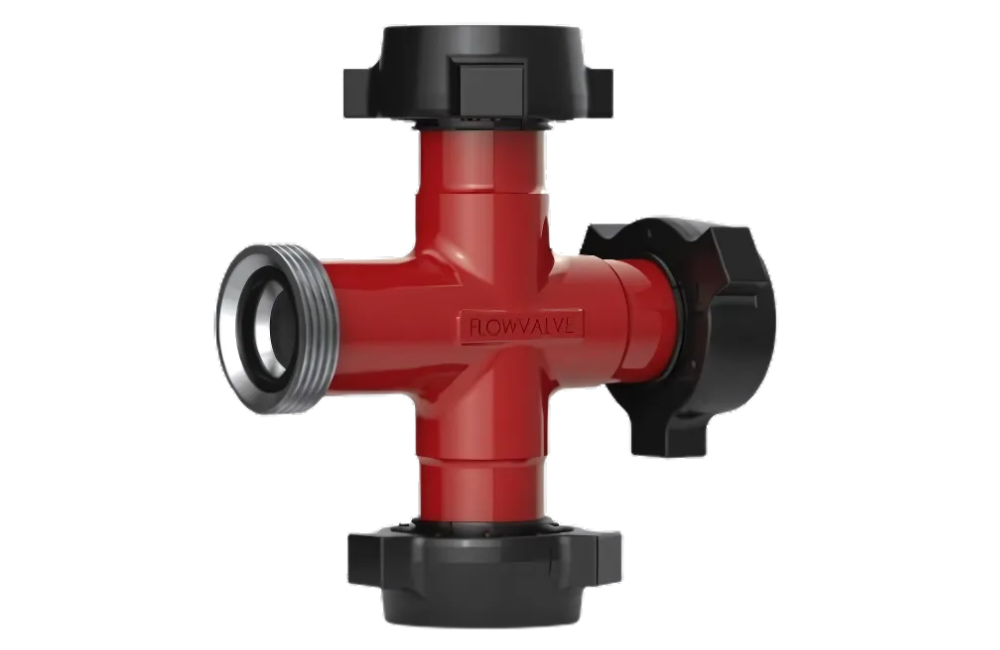
A cross between precision and performance. With precision hammer unions and the best sealing technology available, our crosses are great for applications where an intersecting flow is needed. Each cross is machined from high alloy forged steel that is heat treated for long lasting performance.
Cushion ells
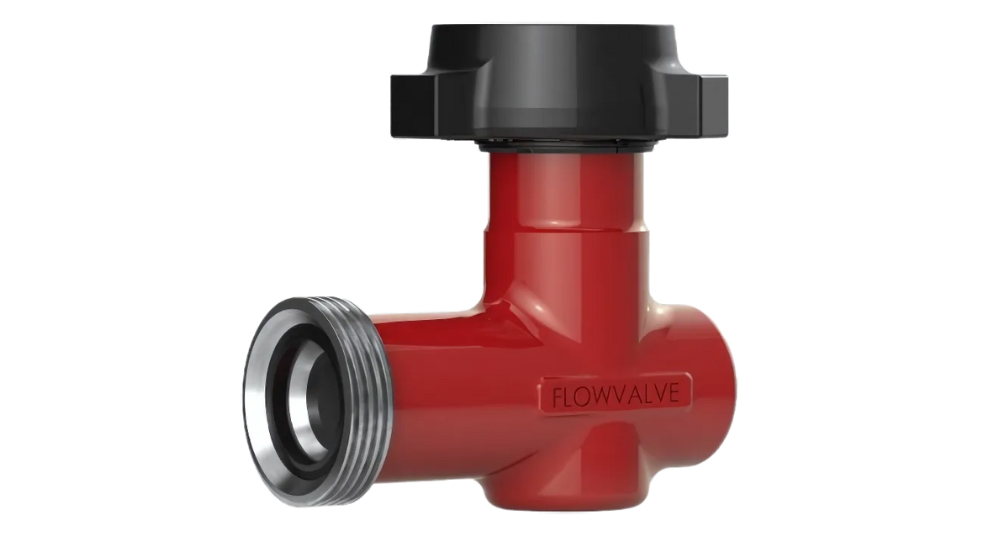
Cushion from the male or female. With extra material at the end of the elbow, our cushion ells are designed for extended service life. This feature behaves as a shock absorber, helping combat wear from abrasive slurry used in high pressure pumping.
Sweep 90’s
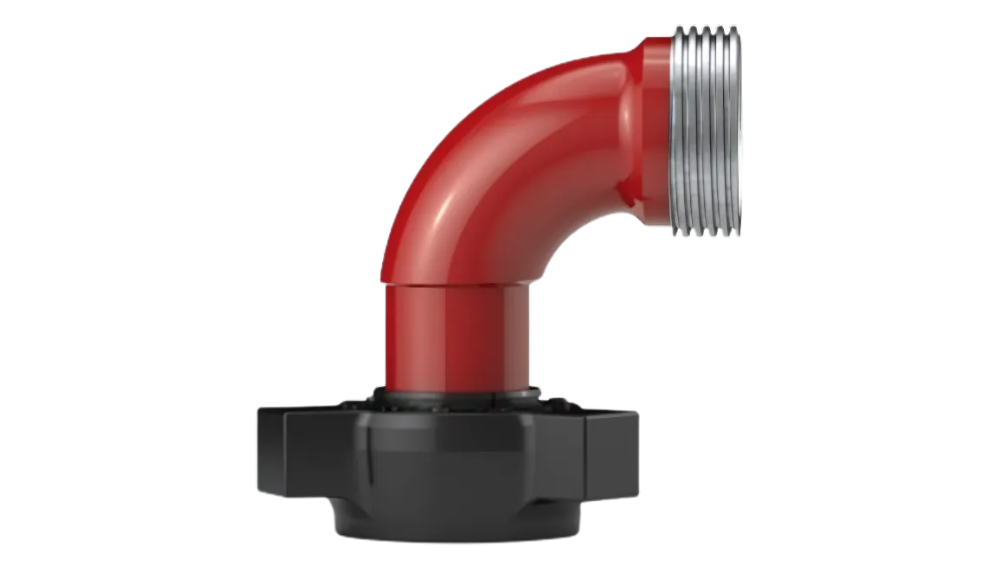
Bent 90 degrees for a smoother flow. With our swivel bending technology, we are able to bend a 90 degree elbow that can be used as an additional option for flowing 90 degrees. Because
of their low wear rate and smoother flow, sweep 90’s are a very popular choice for flowback operations.
Crossovers
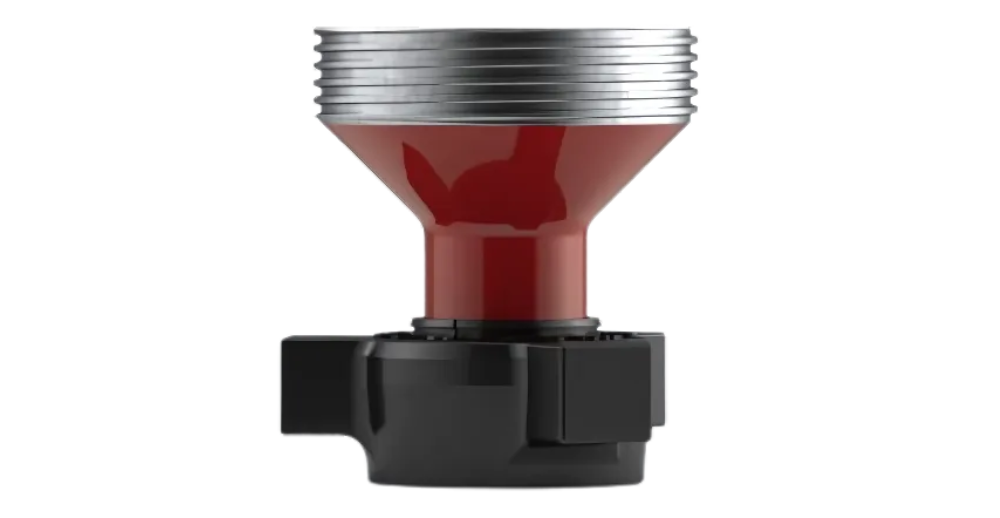
Change over from one size to another. We offer every combination of cross overs in 1”, 1 ½”, 2”, 3” and 4” Fig 1502 and 4” Fig 1002 connections. We carry an assortment of crossovers in stock and can make to order with our state of the art machining cells. We also machine special length crossovers on request.
Laterals
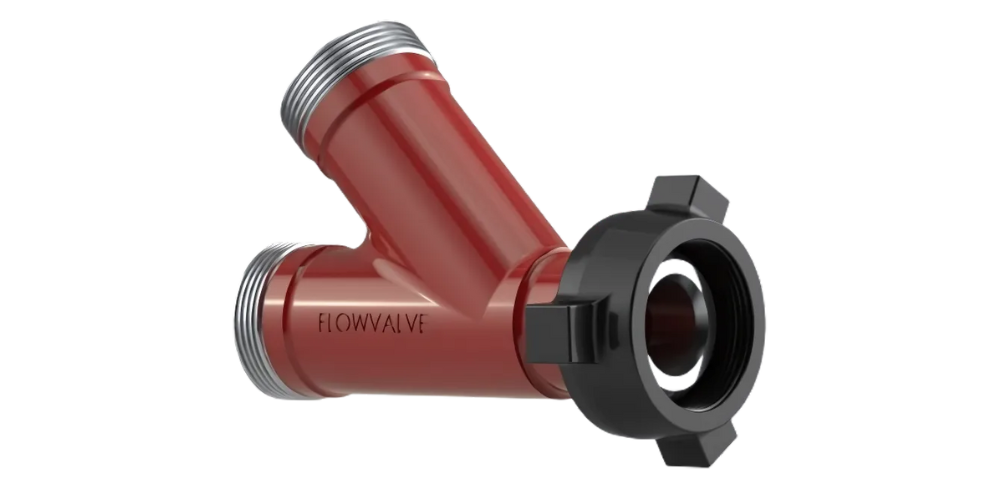
A great way to branch out. Our laterals are frequently used in frac manifolds and other high pressure manifolds. Each lateral is machined from U.S. forged, heat treated steel. They are available in 3” Fig 1502, 4” Fig 1502 and 4” Fig 1002 working pressures with custom end connections to fit your needs.
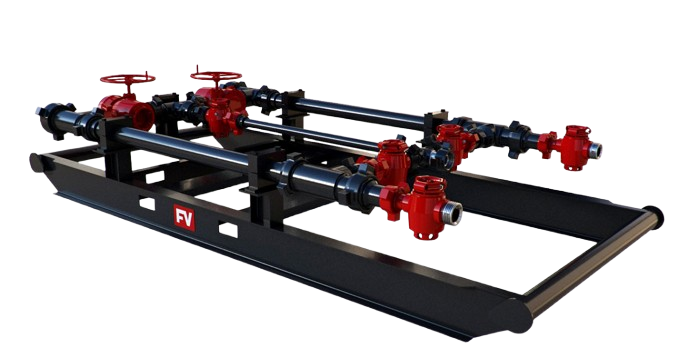
Heavy duty screen system
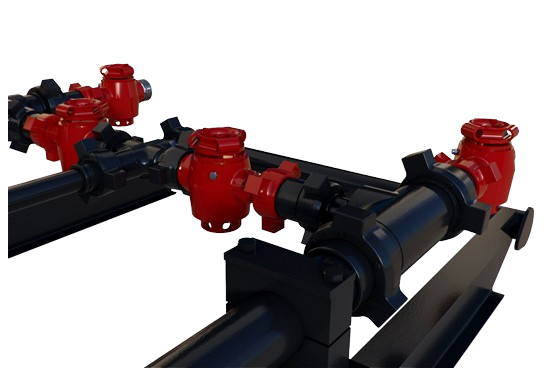
With laser cut slots or holes, our integrated screen system is the best way to catch trash on flow back operations. The screens are threaded on the O.D. to easily detach from the crossover. This makes it amazingly quick and easy to clean out or replace screens when needed.
Rated for 10,000 or 15,000 CWP
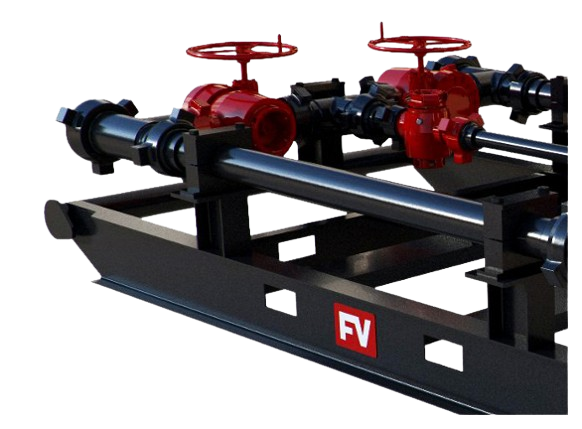
With customizable options, our plugcatchers are rated for 10,000 or 15,000 CWP. Depending on your requirements, we can use different styles of crossovers and pup joints to get the solution you need. We test every one of our plugcatch ers at time and a half CWP before they ship
Flow in. Flow out
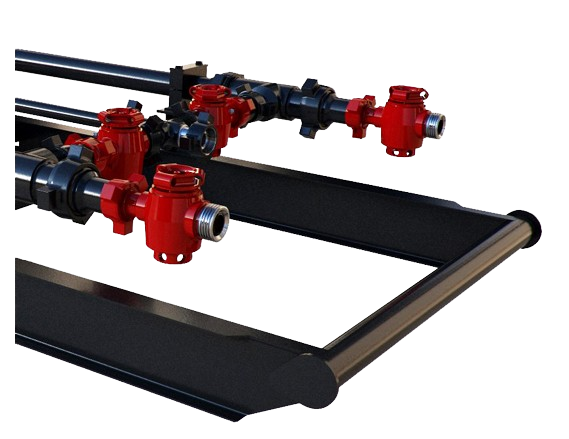
Our standard plugcatcher design flows in at 3” Fig 1502 and flows out at 2” Fig 1502 or 3” Fig 1502 to handle normal flowback operations. Customizable design options are available upon request.
No welds on any high pressure iron.
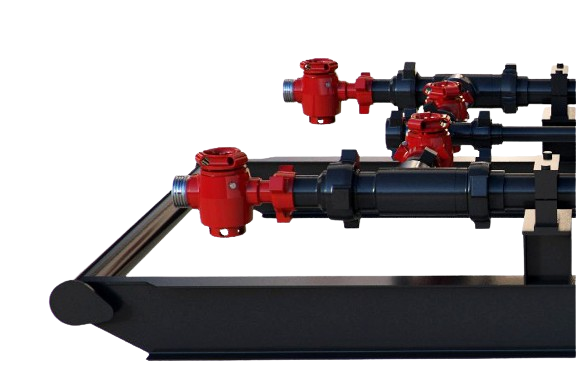
With custom pipe clamps and an innovative thread design for the crossover and screen, our plugcatchers have zero welding on all of the high pressure iron. This safety feature prevents micro cracking that is often found in welding heat treated metals.Bent 90 degrees for a smoother flow. With our swivel bending technology, we are able to bend a 90 degree elbow that can be used as an additional option for flowing 90 degrees. Because of their low wear rate and smoother flow, sweep 90’s are a very popular choice for flowback operations.
Skid mounted
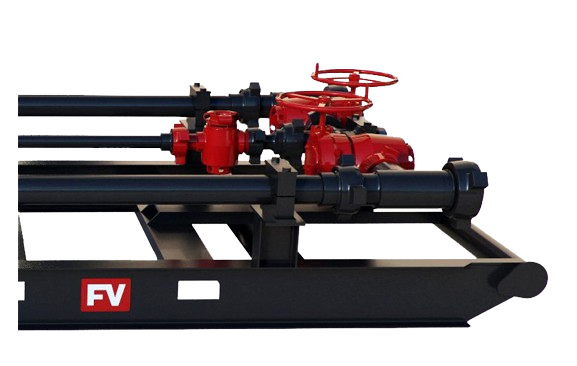
Made for fast rig ups and ease of operation, our plugcatchers are mounted on a skid with heavy duty pipe clamps. With forklift slots designed into the skid, the plugcatcher manifold is easy to load on and off trailers for easy transportation
FLOWVALVE Signature
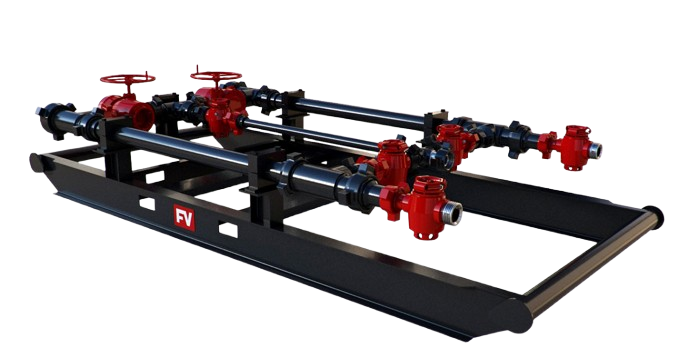
Producing a high performing plugcatcher is easier when you have complete control. Every plugcatcher component has the FLOWVALVE signature, from plug valves, tees, crosses, pup joints and crossovers right down to the skid. When we sign
off on something, we always stand behind it.
Heavy duty screen system
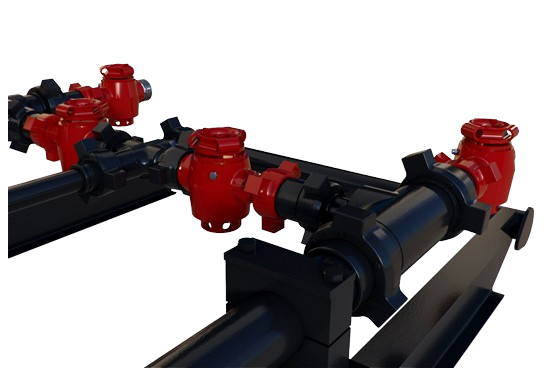
With laser cut slots or holes, our integrated screen system is the best way to catch trash on flow back operations. The screens are threaded on the O.D. to easily detach from the crossover. This makes it amazingly quick and easy to clean out or replace screens when needed.
Rated for 10,000 or 15,000 CWP
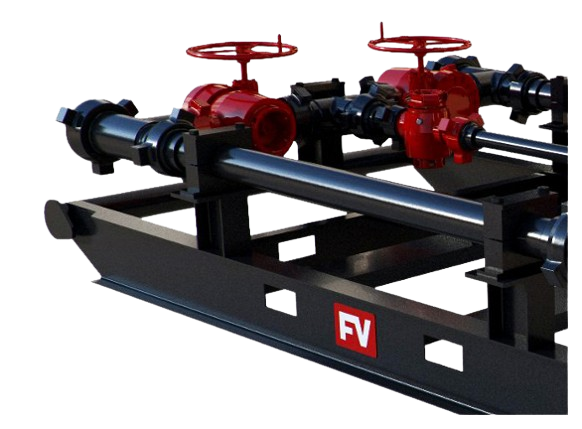
With customizable options, our plugcatchers are rated for 10,000 or 15,000 CWP. Depending on your requirements, we can use different styles of crossovers and pup joints to get the solution you need. We test every one of our plugcatch ers at time and a half CWP before they ship
Flow in. Flow out
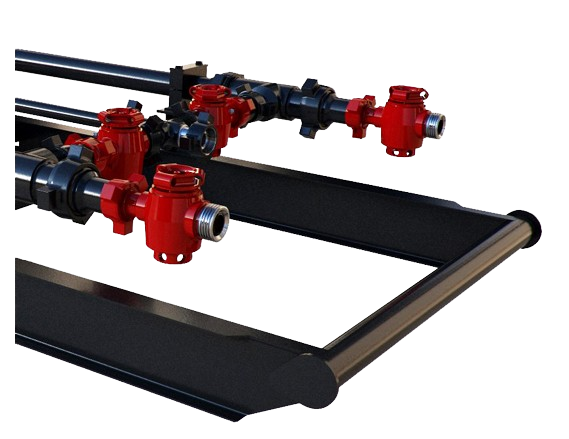
Our standard plugcatcher design flows in at 3” Fig 1502
and flows out at 2” Fig 1502 or 3” Fig 1502 to handle normal flowback operations. Customizable design options are available upon request.
No welds on any high pressure iron.
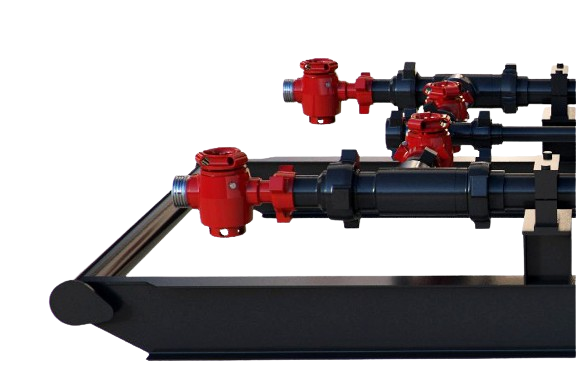
With custom pipe clamps and an innovative thread design for the crossover and screen, our plugcatchers have zero welding on all of the high pressure iron. This safety feature prevents micro cracking that is often found in welding heat treated metals.Bent 90 degrees for a smoother flow. With our swivel bending technology, we are able to bend a 90 degree elbow that can be used as an additional option for flowing 90 degrees. Because of their low wear rate and smoother flow, sweep 90’s are a very popular choice for flowback operations.
Skid mounted
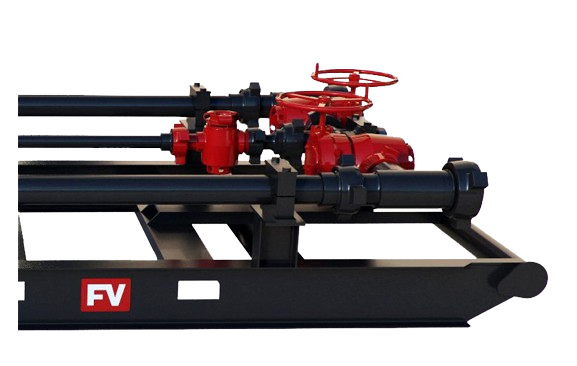
Made for fast rig ups and ease of operation, our plugcatchers are mounted on a skid with heavy duty pipe clamps. With forklift slots designed into the skid, the plugcatcher manifold is easy to load on and off trailers for easy transportation
FLOWVALVE Signature
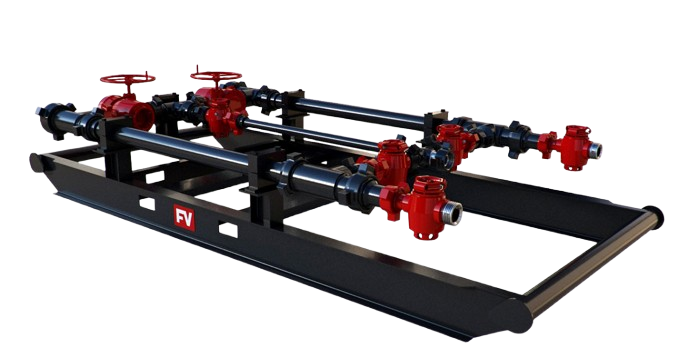
Producing a high performing plugcatcher is easier when you have complete control. Every plugcatcher component has the FLOWVALVE signature, from plug valves, tees, crosses, pup joints and crossovers right down to the skid. When we sign
off on something, we always stand behind it.
Quality is in our name
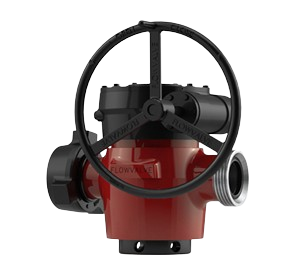
We took all of our experience and packed it into a design that is truly remarkable. From engineering to manufacturing, our plug valves utilize the most advanced manufacturing processes.
Gear up with our gear op
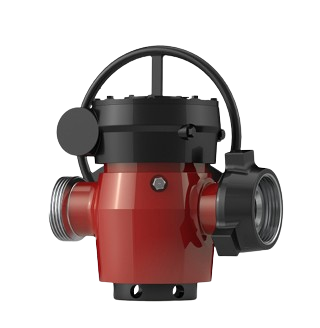
Our gear operated valves are manufactured in house with the same standard of quality as all FlowValve products. FlowValve offers gear operated valves in 3” Fig 1502, 4” Fig 1002 and 4” Fig 1502.
Premium grease for premium results.
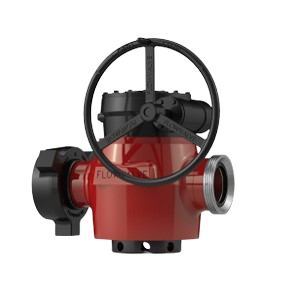
Greasing is very important for the performance of plug valves. Knowing that, we use only the very best grease in our valves during assembly. We also provide the same grease in our plug valve repair kits
From start to FINISH
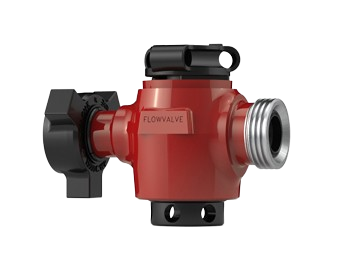
FlowValve plug valve inserts have a RMS finish that is twice as smooth as the industry standard. You can feel the difference
in quality when you actuate a FlowValve plug valve.
Patent pending machining process
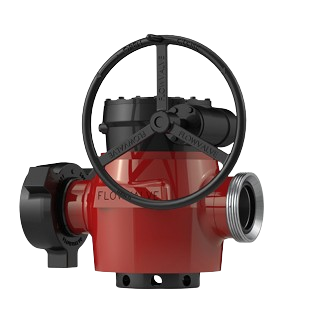
Our patent pending machining process provides us with the ability to make the most precise parts in the industry. The taper of our plug valve is probed with a touch trigger probe. The probe results are analyzed and the CNC machine is adjusted to ensure the parts are machined to the design specifications. Variation has been reduced to microns
Advanced Torque System
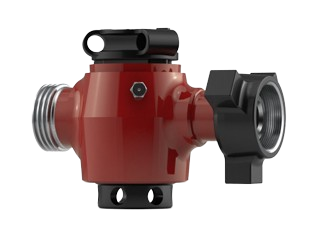
Our advanced torque system ensures that every plug valve adjusting nut is set to an exact torque level. Combine that with our incredible machining processes and you get a product that is consistent. Our design is engineered to give the customer a new level of confidence
Quality is in our name
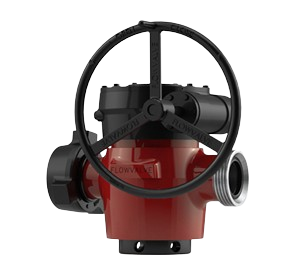
We took all of our experience and packed it into a design that is truly remarkable. From engineering to manufacturing, our plug valves utilize the most advanced manufacturing processes.
Gear up with our gear op
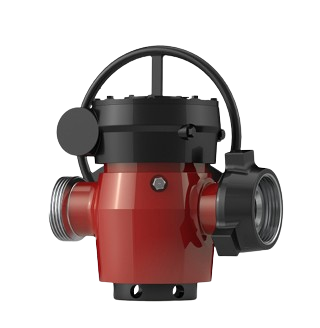
Our gear operated valves are manufactured in house with the same standard of quality as all FlowValve products. FlowValve offers gear operated valves in 3” Fig 1502, 4” Fig 1002 and 4” Fig 1502.
Premium grease for premium results.
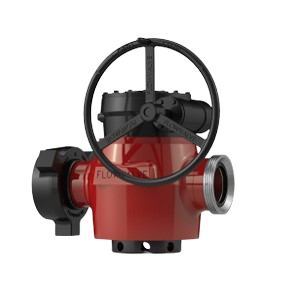
Greasing is very important for the performance of plug valves. Knowing that, we use only the very best grease in our valves during assembly. We also provide the same grease in our plug valve repair kits
From start to FINISH
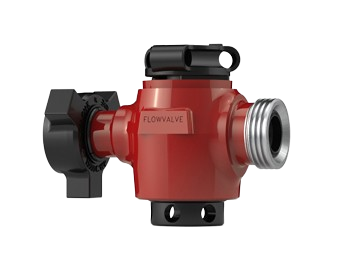
FlowValve plug valve inserts have a RMS finish that is twice as smooth as the industry standard. You can feel the difference
in quality when you actuate a FlowValve plug valve.
Patent pending machining process
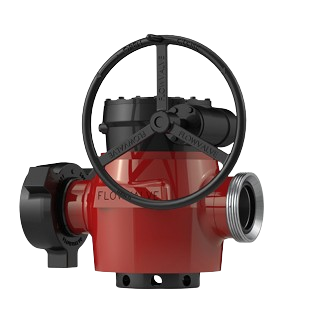
Our patent pending machining process provides us with the ability to make the most precise parts in the industry. The taper of our plug valve is probed with a touch trigger probe. The probe results are analyzed and the CNC machine is adjusted to ensure the parts are machined to the design specifications. Variation has been reduced to microns
Advanced Torque System
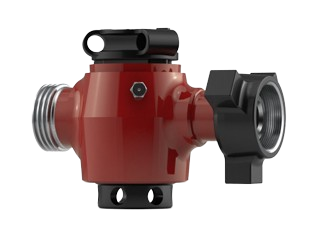
Our advanced torque system ensures that every plug valve adjusting nut is set to an exact torque level. Combine that with our incredible machining processes and you get a product that is consistent. Our design is engineered to give the customer a new level of confidence
A Work of Genius

We took all of our experience and packed it into a design that is truly remarkable. From engineering to manufacturing, our plug valves utilize the most advanced well service technologies. We put together a talented team that produced a work of genius
Plug Valve Perfected
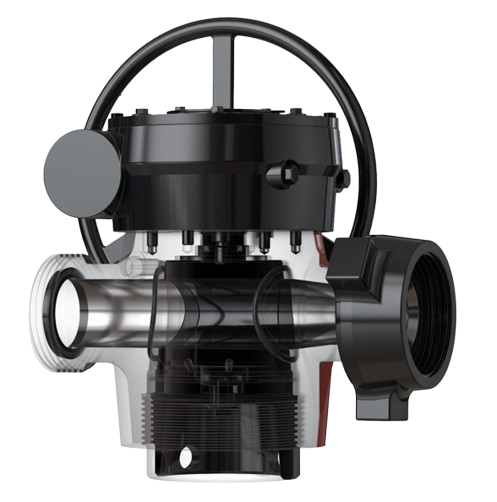
We didn’t try to reinvent the wheel, we perfected it! Our new patent-pending plug valve design removes the most common failure point of traditional plug valve designs. This new innovation adds incredible performance life to the plug valve body. Our new plug valve significantly reduces operating costs
Paradigm Shift
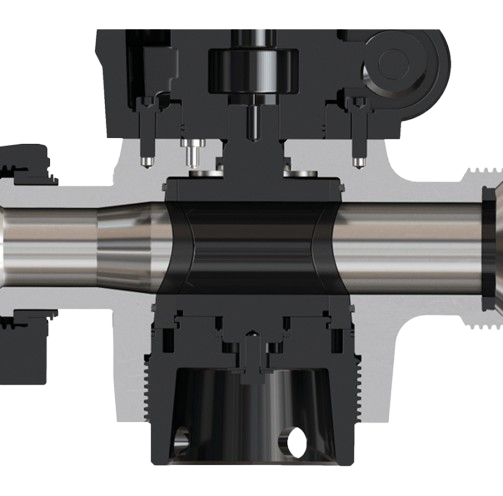
Most plug valves fail at the sealing surface inside the body of the plug valve. This is where the body seals against the O-ring installed into the insert. Over time, the sealing surface of the body wears out and loses its ability to hold pressure. Our patent-pending design removes this issue by transferring the seal groove from the plug valve inserts to the plug valve body
SUPER SEAL TECHNOLOGY
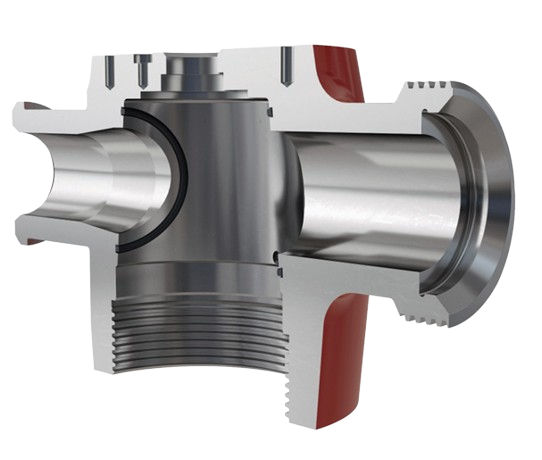
When we reinvented the plug valve, we didn’t stop at the groove. We designed a new seal to exclusively handle the extreme services of plug valves. The Super Seal™ was engineered with a proprietary elastomer that outperforms the standard O-ring used in traditional plug valves. The Super Seal™ is molded to snap right into the plug valve body groove, making assembly simple and easy
Brand New Sealing Surface in Every Kit
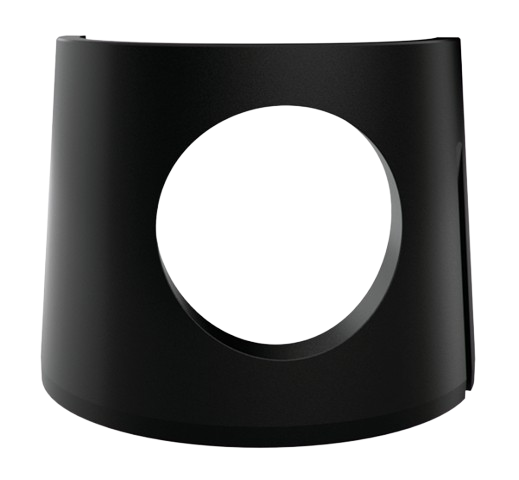
Our patent-pending Grooveless Inserts™ were reimagined for performance. The outside diameter of the insert now seals against the Super Seal™ that’s installed in the body of the plug valve. This new design transfers the wear from the plug valve body to the replaceable inserts. Now every time you rebuild a plug valve you get a brand new sealing surface
Patent-Pending iPAR Quality System
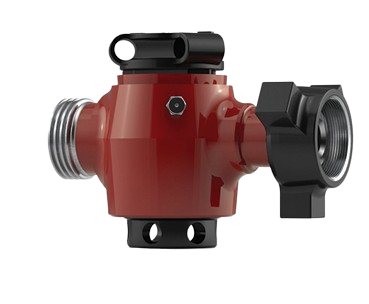
Our patent-pending iPAR quality system helps us make the most precise parts in the industry. A touch trigger probe measures the taper on our plug valves and results are analyzed by the machine. Measurements are made in microns. No one else can offer this much precision
Premium Grease for Premium Results
Greasing is very important for the performance of plug valves. Knowing that, we use only the best grease in our valves during assembly. We also provide the same grease in our plug valve repair kits. Our decision to use the very best makes all the
difference
Advanced Torque System
Each plug valve adjusting nut is set to an exact torque level with our advanced torque system. Combined with our
innovative manufacturing technologies, this assembly procedure produces parts that are always reliable. This
process design was engineered to ensure a new level of confidence
Gear Up with Our Gear Op
FlowValve gear operated valves are manufactured in-house with the same standard of quality as all our products. FlowValve offers gear operated valves in: 3” Fig 1502, 4” Fig 1002 and 4” Fig 1502
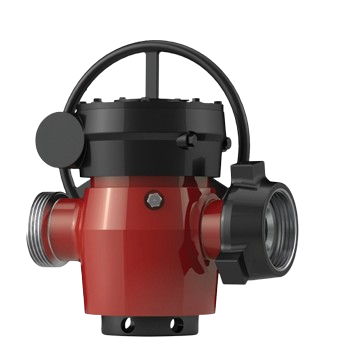
A Work of Genius

We took all of our experience and packed it into a design that is truly remarkable. From engineering to manufacturing, our plug valves utilize the most advanced well service technologies. We put together a talented team that produced a work of genius
Plug Valve Perfected
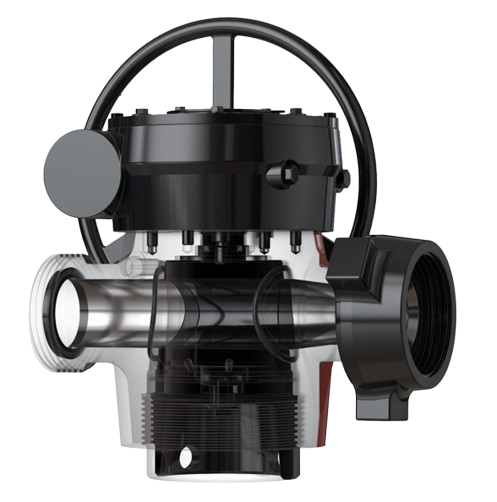
We didn’t try to reinvent the wheel, we perfected it! Our new patent-pending plug valve design removes the most common failure point of traditional plug valve designs. This new innovation adds incredible performance life to the plug valve body. Our new plug valve significantly reduces operating costs
Paradigm Shift
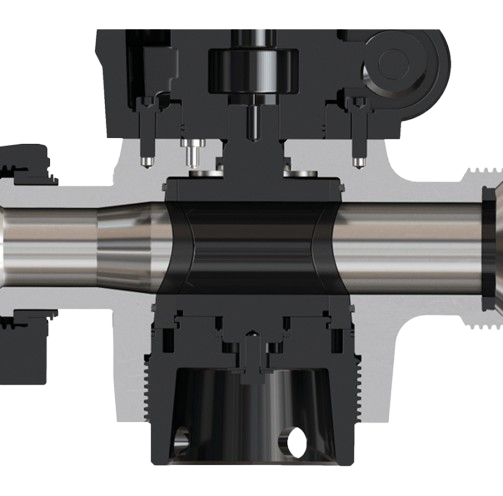
Most plug valves fail at the sealing surface inside the body of the plug valve. This is where the body seals against the O-ring installed into the insert. Over time, the sealing surface of the body wears out and loses its ability to hold pressure. Our patent-pending design removes this issue by transferring the seal groove from the plug valve inserts to the plug valve body
SUPER SEAL TECHNOLOGY
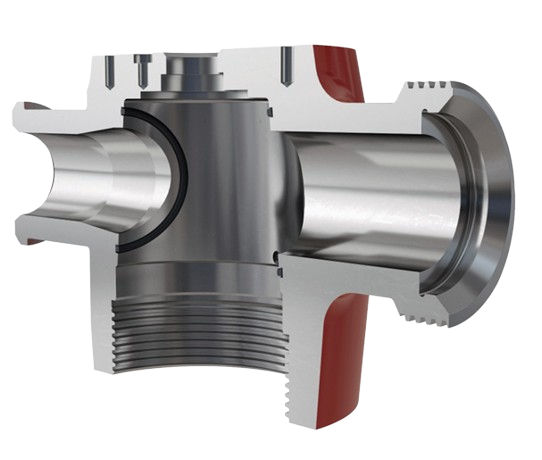
When we reinvented the plug valve, we didn’t stop at the groove. We designed a new seal to exclusively handle the extreme services of plug valves. The Super Seal™ was engineered with a proprietary elastomer that outperforms the standard O-ring used in traditional plug valves. The Super Seal™ is molded to snap right into the plug valve body groove, making assembly simple and easy
Brand New Sealing Surface in Every Kit
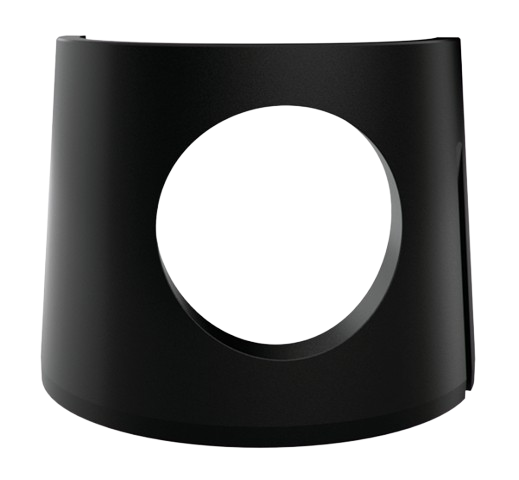
Our patent-pending Grooveless Inserts™ were reimagined for performance. The outside diameter of the insert now seals against the Super Seal™ that’s installed in the body of the plug valve. This new design transfers the wear from the plug valve body to the replaceable inserts. Now every time you rebuild a plug valve you get a brand new sealing surface
Patent-Pending iPAR Quality System
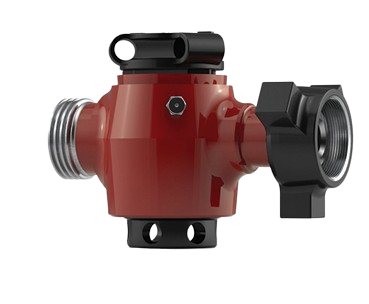
Our patent-pending iPAR quality system helps us make the most precise parts in the industry. A touch trigger probe measures the taper on our plug valves and results are analyzed by the machine. Measurements are made in microns. No one else can offer this much precision
Premium Grease for Premium Results
Greasing is very important for the performance of plug valves. Knowing that, we use only the best grease in our valves during assembly. We also provide the same grease in our plug valve repair kits. Our decision to use the very best makes all the
difference
Advanced Torque System
Each plug valve adjusting nut is set to an exact torque level with our advanced torque system. Combined with our
innovative manufacturing technologies, this assembly procedure produces parts that are always reliable. This
process design was engineered to ensure a new level of
confidence
Gear Up with Our Gear Op
FlowValve gear operated valves are manufactured in-house with the same standard of quality as all our products. FlowValve offers gear operated valves in: 3” Fig 1502, 4” Fig 1002 and 4” Fig 1502
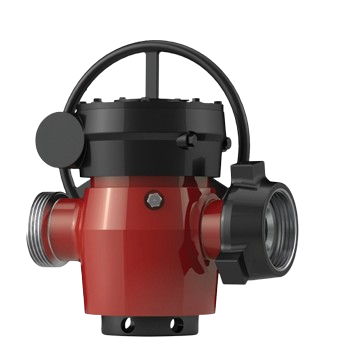
Our swivels... Last longer
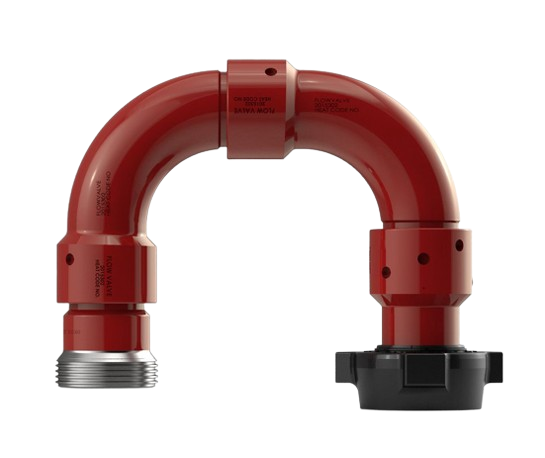
Ourswivels last longer than any other brand in the world. We have conducted several rigorous field tests and each one has concluded that FlowValve outperforms everyone in the categories of wear, durability and overall performance. One competitor even stated that FlowValve outperformed them by up to 200%. It does not take long to tell they truly are an incredible product… unless you are waiting for them to wear out.
Heat treated to the highest stan dards.
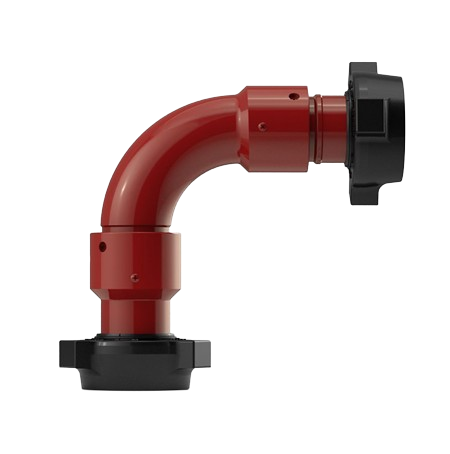
Our heat treat process has been refined and dialed in to give our swivels the ultimate durability. Our high hardness yet extraordinary tensile yield gives FlowValve swivels a unique combination of strength and durability without sacrificing ductility. Each swivel joint is heat treated and case hardened to withstand the toughest well service environments
Design analysis review
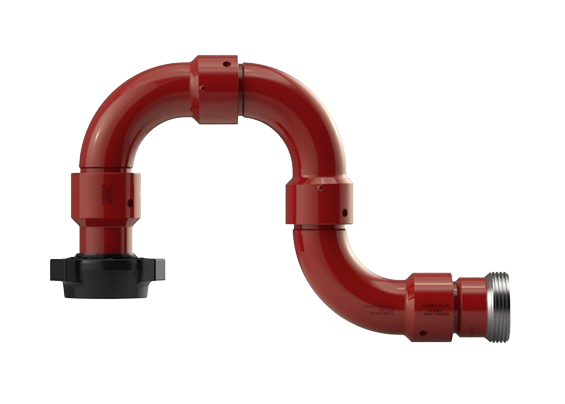
Our licensed engineers have conducted a complete design analysis review on our swivel joints. By using tools such as finite element analysis and non-destructive testing, we have proven that our swivels will perform as they are designed. Our extraordinary attention to detail ensures that the dimensions and specifications have been proven to perform the job at the highest level.
Advanced bending technology
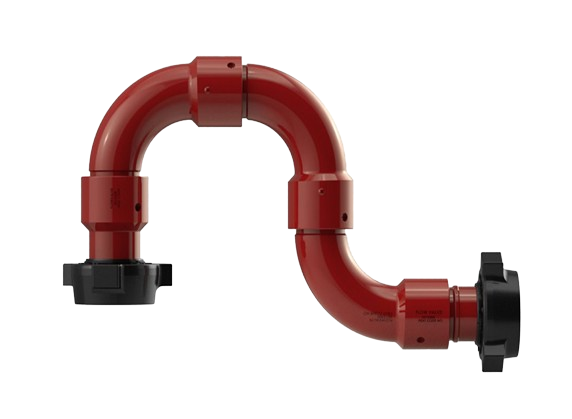
It all begins with a perfect bend. That is what makes great swivel joints great. We have invented a process that is one of the most innovative and complex in the industry. This process gives us the ability to continuously make a consistent bend. This repeatable bend creates a concentric through-bore which minimizes turbulence, creates a smoother flow, and reduces wear. We are committed to “bending” over backwards for our customers.
Patented machining process
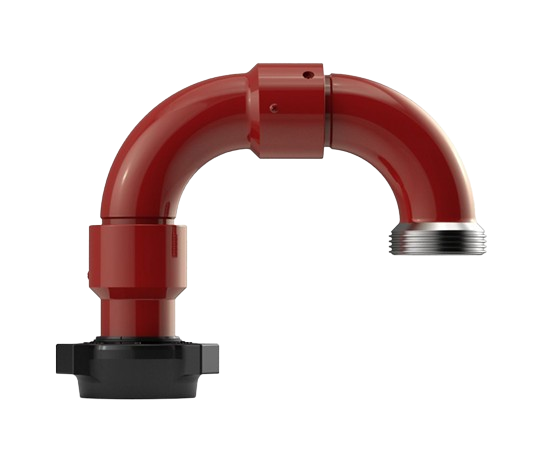
Our patented machining process was designed to help us leapfrog the industry in production efficiency. We have achieved cycle times that are unmatched in swivel production. Our process is also more stable than traditional machining and bending methods. This breakthrough technology is unlike anything ever used before.
Winning the “race.”
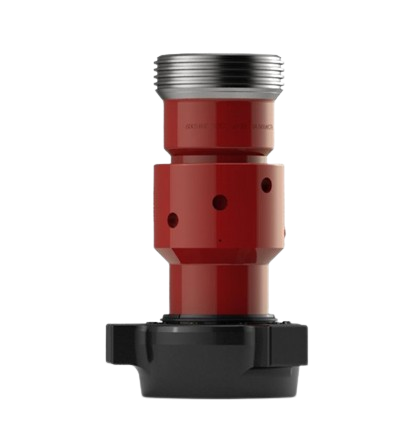
Our advanced ball races are designed to give superior strength
and movability. Our ball races are machined and measured with an intuitive manufacturing process developed at FlowValve. This patent pending process meticulously analyzes the part on a CNC machine and gives instantaneous feedback to the machinist. This enables us to measure our ball races in microns. No one else can offer this much precision or this much reliability.
Our swivels... Last longer
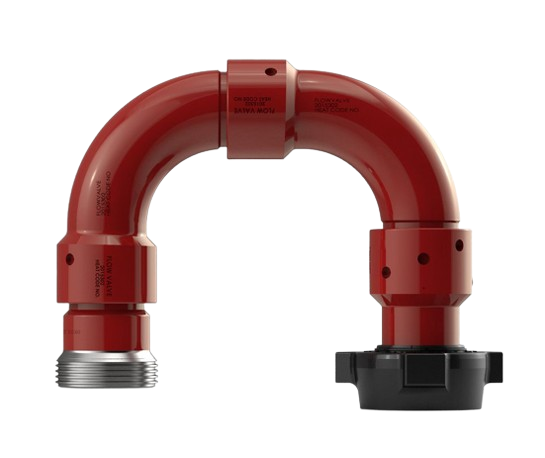
Ourswivels last longer than any other brand in the world. We have conducted several rigorous field tests and each one has concluded that FlowValve outperforms everyone in the categories of wear, durability and overall performance. One competitor even stated that FlowValve outperformed them by up to 200%. It does not take long to tell they truly are an incredible product… unless you are waiting for them to wear out.
Heat treated to the highest stan dards.
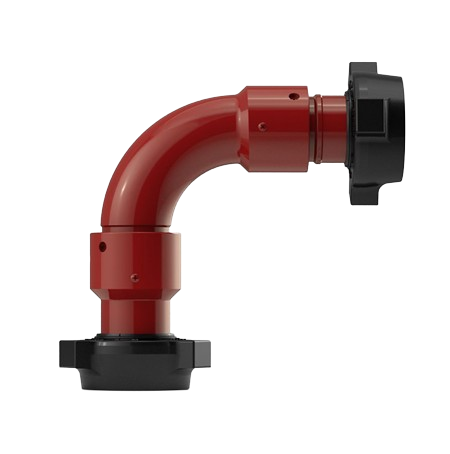
Our heat treat process has been refined and dialed in to give our swivels the ultimate durability. Our high hardness yet extraordinary tensile yield gives FlowValve swivels a unique combination of strength and durability without sacrificing ductility. Each swivel joint is heat treated and case hardened to withstand the toughest well service environments
Design analysis review
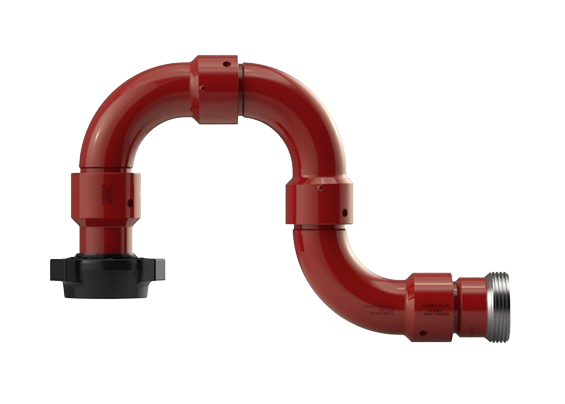
Our licensed engineers have conducted a complete design analysis review on our swivel joints. By using tools such as finite element analysis and non-destructive testing, we have proven that our swivels will perform as they are designed. Our extraordinary attention to detail ensures that the dimensions and specifications have been proven to perform the job at the highest level.
Advanced bending technology
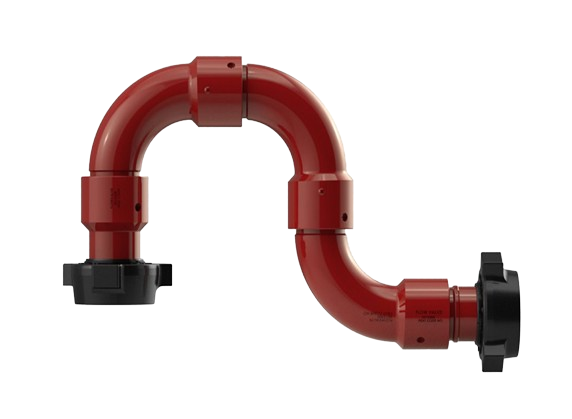
It all begins with a perfect bend. That is what makes great swivel joints great. We have invented a process that is one of the most innovative and complex in the industry. This process gives us the ability to continuously make a consistent bend. This repeatable bend creates a concentric through-bore which minimizes turbulence, creates a smoother flow, and reduces wear. We are committed to “bending” over backwards for our customers.
Patented machining process
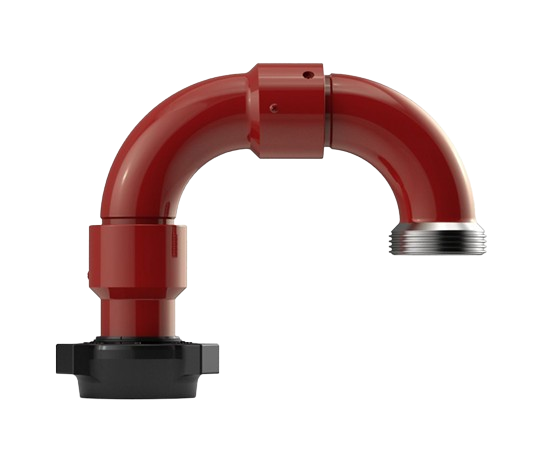
Our patented machining process was designed to help us leapfrog the industry in production efficiency. We have achieved cycle times that are unmatched in swivel production. Our process is also more stable than traditional machining and bending methods. This breakthrough technology is unlike anything ever used before.
Winning the “race.”
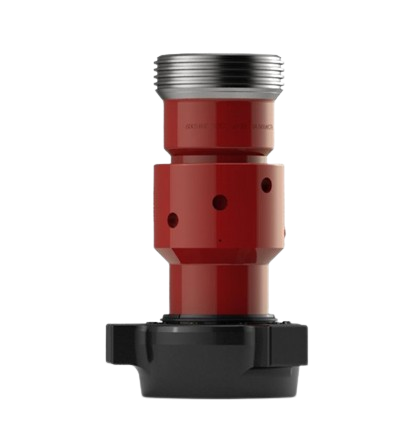
Our advanced ball races are designed to give superior strength
and movability. Our ball races are machined and measured with an intuitive manufacturing process developed at FlowValve. This patent pending process meticulously analyzes the part on a CNC machine and gives instantaneous feedback to the machinist. This enables us to measure our ball races in microns. No one else can offer this much precision or this much reliability.