KERR Pumps
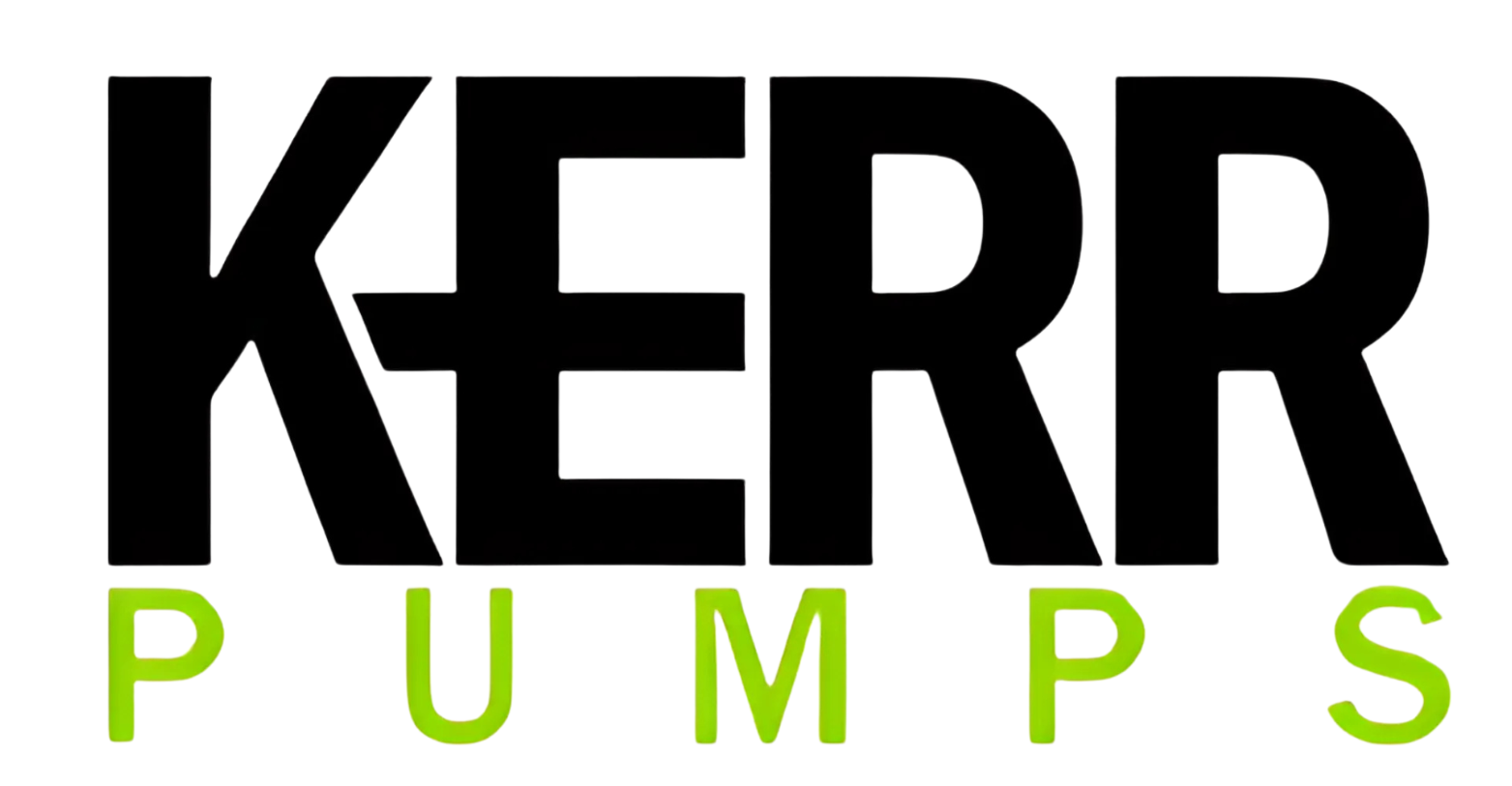
- Introduction
- Fracking Pumps
- Fluid Ends
- Plunger and piston Pumps
- Spare Parts
- Type of Pumps
One Kerr Pump: Built to Power, Engineered to Last!
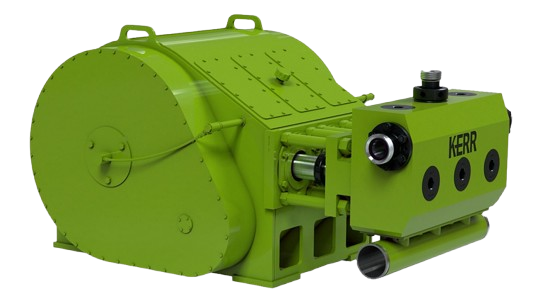
Since its founding in 1946, Kerr Pumps Corporation has been a leader in delivering reliable, high-performance pumps to the oil and gas industry. Originally based in Ada, Oklahoma, Kerr Pumps relocated to Sulphur, Oklahoma in 1992 to support its growth and improve access to major transportation routes. Under new ownership in 1996, the company expanded its product line to serve a variety of industrial applications, earning its reputation as one of the top manufacturers of FRAC pumps globally, renowned for exceptional quality.
One Roof, One Vision
At Kerr Pumps, every step of the production process—from design and engineering to machining, assembly, and testing—occurs under one roof at our state-of-the-art facility in Sulphur, Oklahoma. This unified approach fosters seamless collaboration, efficient problem-solving, and faster response times, giving Kerr Pumps an unmatched advantage in the industry.
Breakthrough Technology: iPAR™ and PQC™
Kerr Pumps leads the way in innovation with our patent-pending iPAR™ (in-Process Automatic Recalibration™) technology. Unlike traditional CNC machines that can lose calibration due to coordinate drift, iPAR™ automatically detects deviations and recalibrates in real-time, ensuring unparalleled precision. This revolutionary technology powers our Programmable Quality Control™ (PQC™) system, where quality is integrated directly into the manufacturing process, not inspected after the fact. Developed over two years, PQC™ eliminates defects by embedding quality at every stage of production.
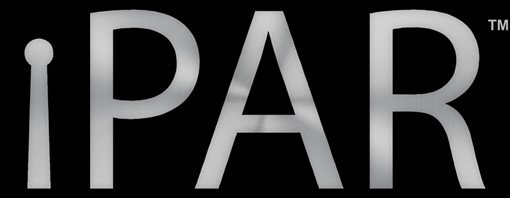
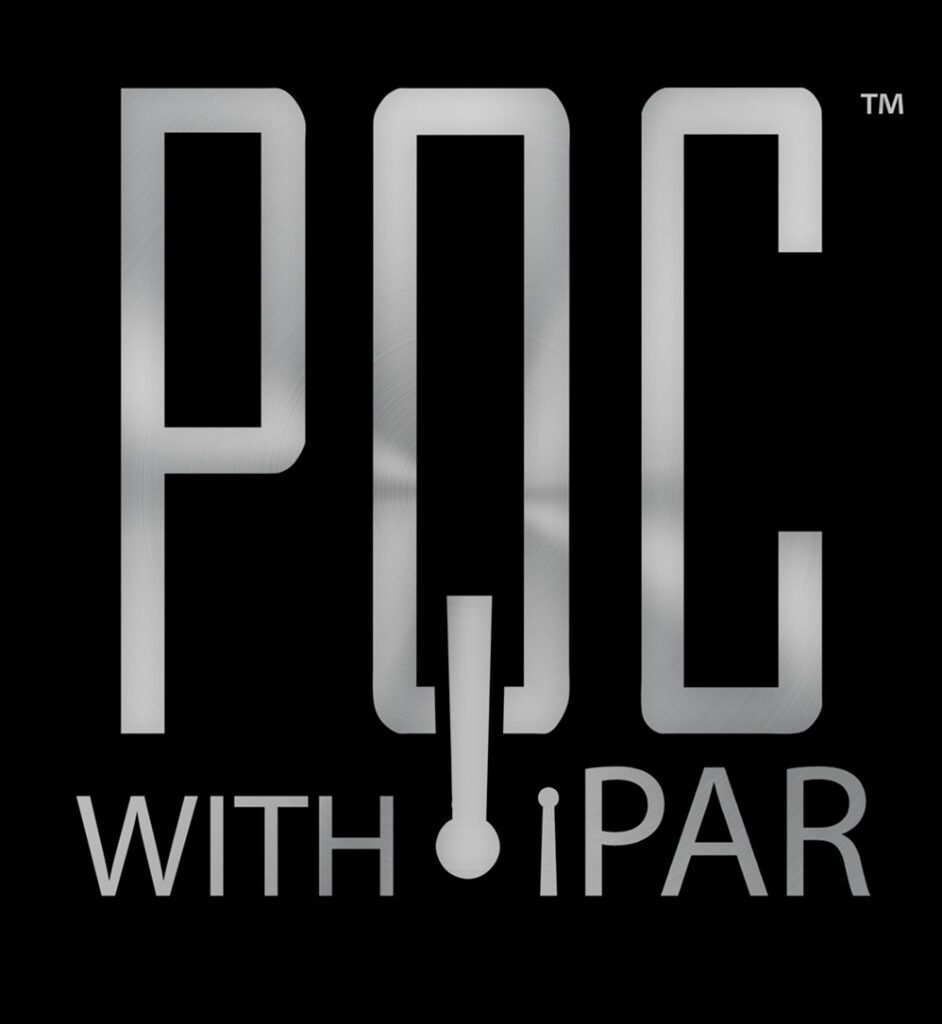
Kerr Pumps: Redefining Durability and Precision, Delivering Power That Never Quits!
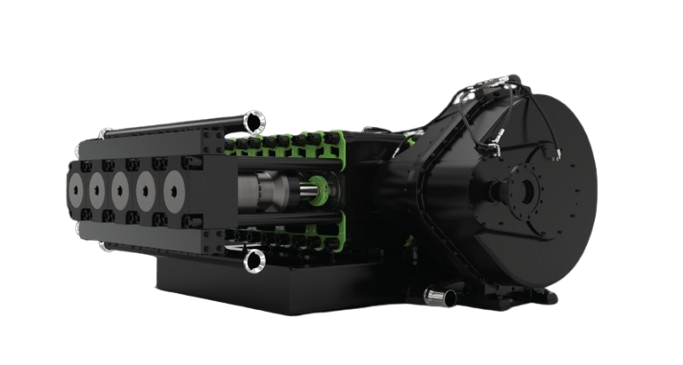
The EF5 well service pump is designed to exceed the demands of the pressure pumping and stimulation in-dustry. The first of its kind, the EF5 is engineered for continuous duty frac and solves the common failure modes associated with traditional reciprocating pump designs.
The EF5 is comprised of modular subassemblies making up the power frame, gear box, and fluid ends. These independent subassemblies ensure easy maintenance and maximum performance, while providing peak longevity.
Need The Perfect Pump?
Select Your PSI and GPM - Let Kerr Match You with the Ultimate Solution!
Power End
The power frame consists of an integrally cast crankshaft housing, and independently cast crosshead guides, compressed between forged alloy steel plates via KERR’s patent-pending Thru-Rods. This “No-Weld” frame system eliminates the frame cracking commonly associated with traditional fabricated power frames and re-duces power frame flexure by 90% versus legacy equipment. The Thru-Rods are pre-loaded with a hydraulic tensioning tool to prevent cyclic loading and maximize fatigue life.
The patent-pending connecting rod / cross head design eliminates the bushings traditionally used on the con-necting rod knuckles, instead making use of fully cylindrical roller bearings. These full sized roller bearings minimize unit loading during operation and more reliably lubricate – even in the event of compromised discharge valves. This design also transfers wear away from the connecting rod to a replaceable, automotive style, wrist pin.
Gearing
The EF5 is driven by a single 16.6” wide herringbone bull gear and pinion at a 6.286:1 ratio. The single sided bull gear prevents torsional deflection in the pinion shaft and more efficiently transfers torque to the crank-shaft. Each gear has its own pair of roller bearings and does not rely on crank center main bearings to carry gear box loads. The bull and pinion are located in an isolated cast housing with mounting feet preventing overhung loads.
Fluid End
The EF5 replaces the traditional fluid end with 5 modular in-line “Vortex” fluid end pods. Each pod is com-prised of one suction valve, one discharge valve, and one shared two-sided seat – all parallel with the plunger bore. KERR’s replaceable packing sleeve is incorporated into the fluid end pod with a reduced number of parts and an increased safety factor. Each pod is further optimized to isolate cyclic fatigue away from inter-secting bores and eliminate reciprocating seal wear.
With only one entry point and no interference fit on the single seat, failure modes have been eliminated, maintenance has been simplified, and the number of parts and tools has been reduced.
Frac One Connect - F1X
The Most Technologically Advanced Fluid End
Kerr Pumps’ patent-pending Frac One CONNECT Fluid End will bolt right up to your existing stay rods with a more rigid, flangeless design.
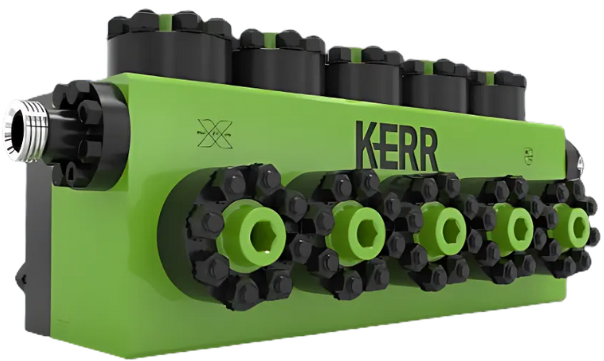
Frac One Connect - F1X
The Most Technologically Advanced Fluid End
Kerr Pumps’ patent-pending Frac One CONNECT Fluid End will bolt right up to your existing stay rods with a more rigid, flangeless design.
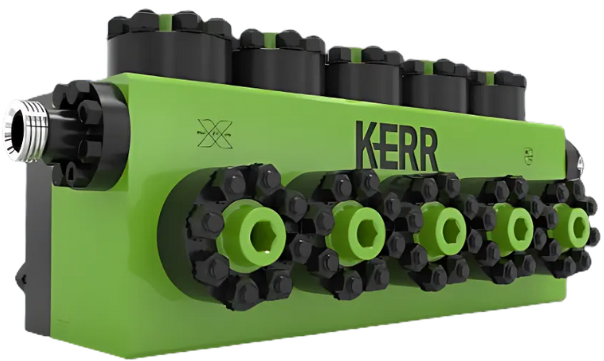
Frac One CONNECT is the best fluid end we have ever manufactured, and ships with these technologies:
Super Stainless II
The strongest stainless steel ever used for a Frac Fluid End.
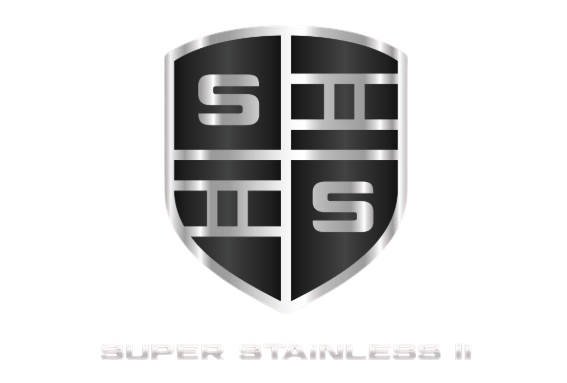
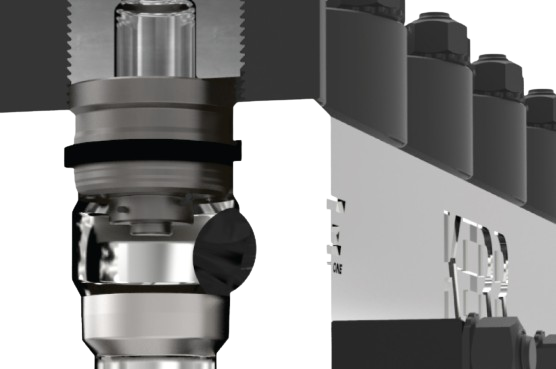
Super Seal Design
Replaceable stuffing box sleeves with all seals embedded into the fluid end to prevent washouts.
Tungsten Super Seat
Tungsten carbide valve seats are designed to protect the fluid end from valve seat deck washouts. These seats last up to ten times longer than traditional valve seats!
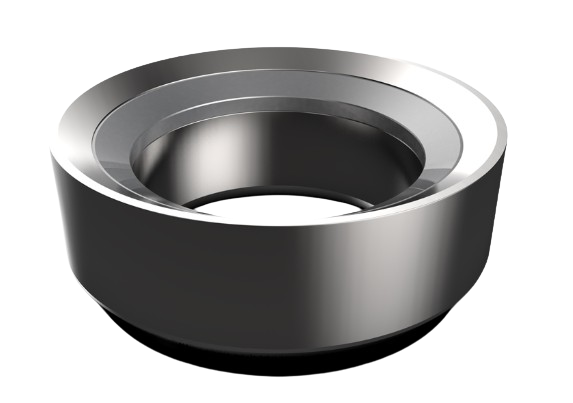
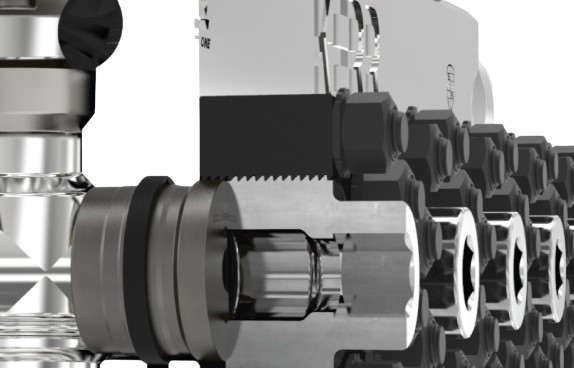
Frac One System
Our patent-pending Frac One X bolt on threaded retainers are for replacement of stuck retainer and packing nuts by unbolting the assembly box. It also has the speed and performance of a threaded retainer nut.
Super Stainless II
The strongest stainless steel ever used for a Frac Fluid End.
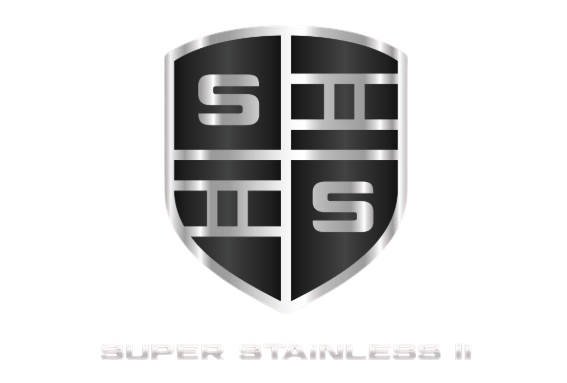
Super Seal Design
Replaceable stuffing box sleeves with all seals embedded into the fluid end to prevent washouts.
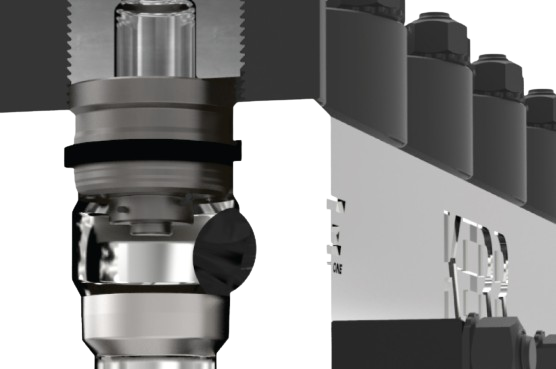
Tungsten Super Seat
Tungsten carbide valve seats are designed to protect the fluid end from valve seat deck washouts. These seats last up to ten times longer than traditional valve seats!
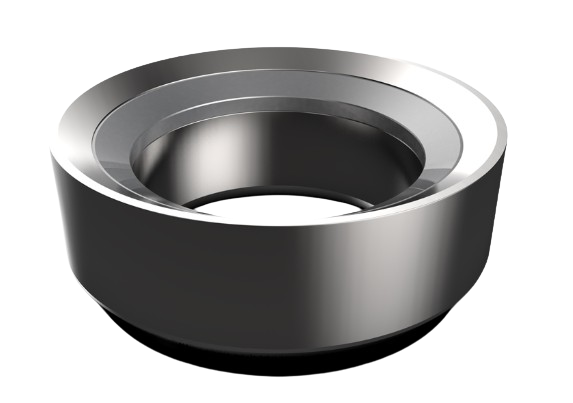
Frac One System
Our patent-pending Frac One X bolt on threaded retainers are for replacement of stuck retainer and packing nuts by unbolting the assembly box. It also has the speed and performance of a threaded retainer nut.
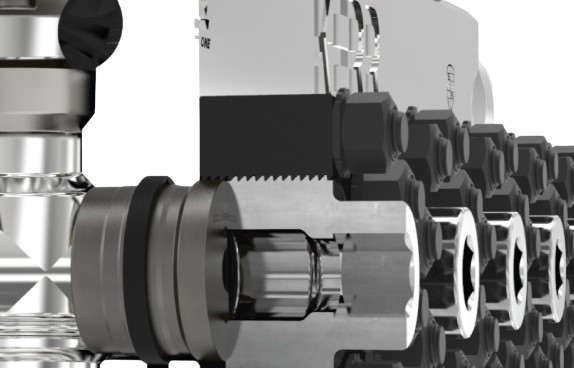
- Fluid End type
- 7 Failure in Fluid End
Need The Perfect Fuild Ends?
Select Your PSI and GPM - Let Kerr Match You with the Ultimate Solution!
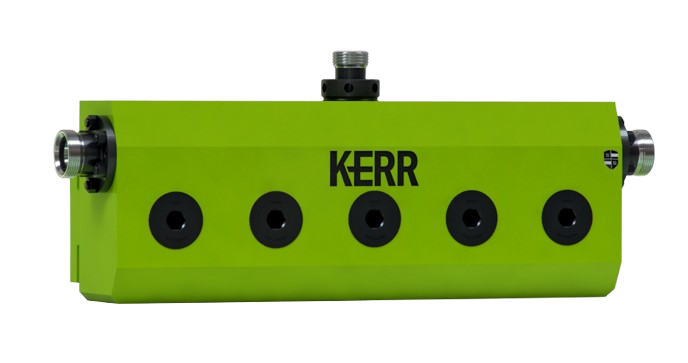
QWS2500HD
Stroke: 8 Inches
Materials:
Super Stainless™
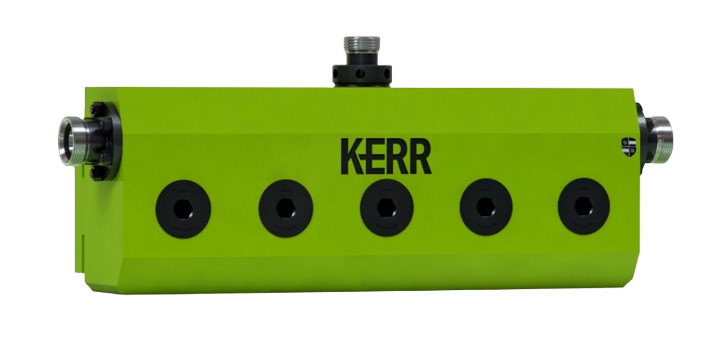
PLUNGER SIZE
4″
4.5″
5″
6″
6.5″
PSI
17,905
14,147
11,459
7,958
6,781
GPM
718
909
1,122
1,616
1,896
BPM
17.1
21.6
26.7
38.5
45.1
TWS2500HD
Stroke: 8 Inches
Materials:
Super Stainless™
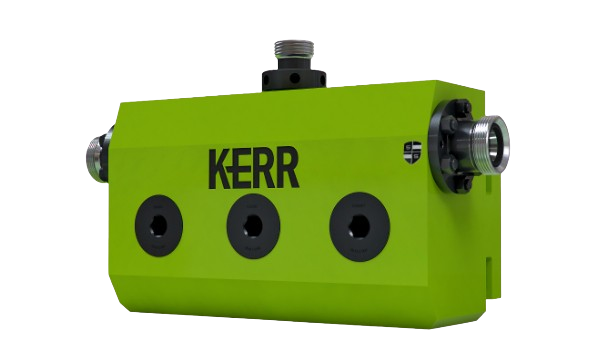
PLUNGER SIZE
4″
4.5″
5″
5.5″
6″
6.5″
PSI
17,905
14,147
11,459
9,470
7,958
6,781
GPM
431
545
673
815
969
1,138
BPM
10.2
12.9
16
19.4
23.1
27.1
QWS1000S
Stroke: 6 Inches
Materials:
Super Stainless™
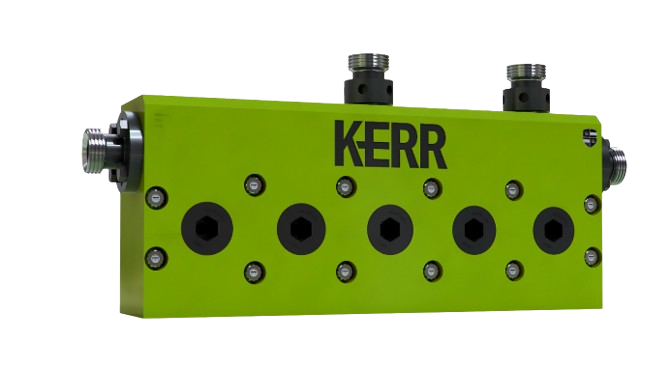
PLUNGER SIZE
2.75″
3″
3.5″
4″
4.5″
PSI
15,000
15,000
10,394
7,958
6,288
GPM
347
413
562
734
929
BPM
8.3
9.8
13.4
17.5
22.1
TWS600S
Stroke: 6 Inches
Materials:
Super Stainless™
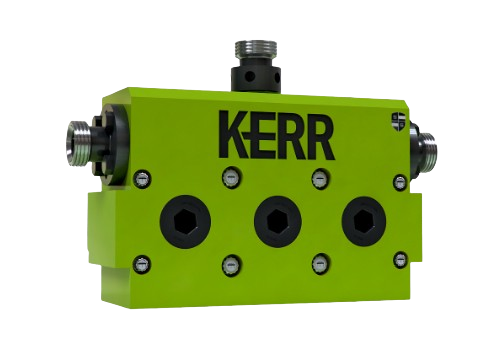
PLUNGER SIZE
2.75″
3″
3.5″
4″
4.5″
PSI
16,832
14,147
10,384
7,958
6,288
GPM
208
248
337
441
588
BPM
5
5.9
8
10.5
13.3
T60WS
Stroke: 6 Inches
Materials:
Super Stainless™
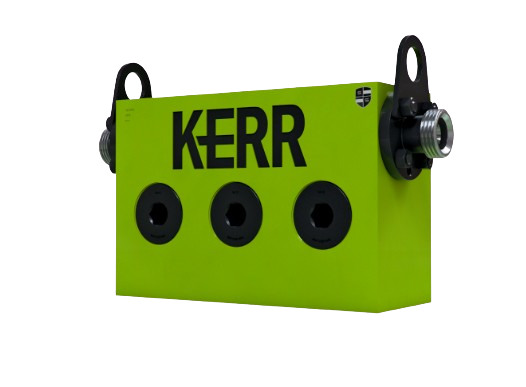
PLUNGER SIZE
3″
3.5″
4″
4.5″
PSI
12,000
8,817
6,750
5,333
GPM
207
281
367
465
BPM
4.9
6.7
8.7
11.1
Don't Let the 7 Failure Hold You Back- Experience Kerr Pumps Superior Design
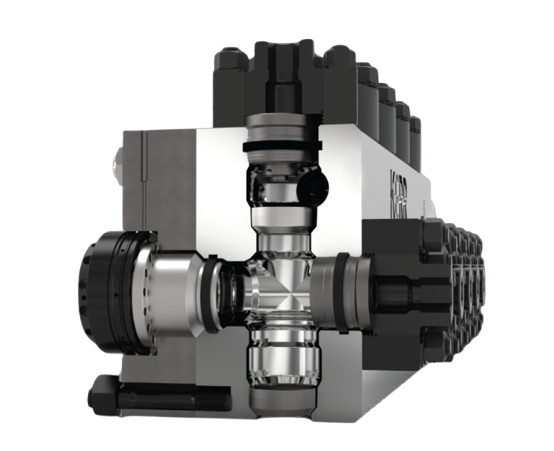
Failure 01
Intersecting Bore Cracking
Intersecting bore cracking was the number one failure for fluid ends until we cracked the code. Kerr Pumps fluid ends are built to frac! Made with Super Stainless II – the strongest and toughest stainless steel ever used in a fluid end – each Kerr Super Stainless fluid end model is engineered with proprietary stress reducing geometries that are optimized to withstand the highest loads in the industry. All of these Transfer the Wear™ design benefits are all available in our all new patent-pending Frac One Connect fluid end!
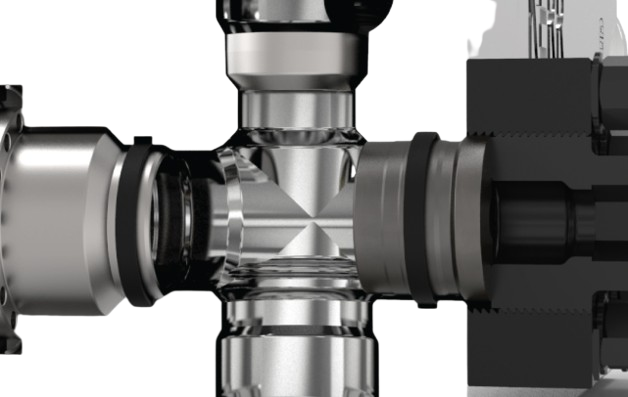
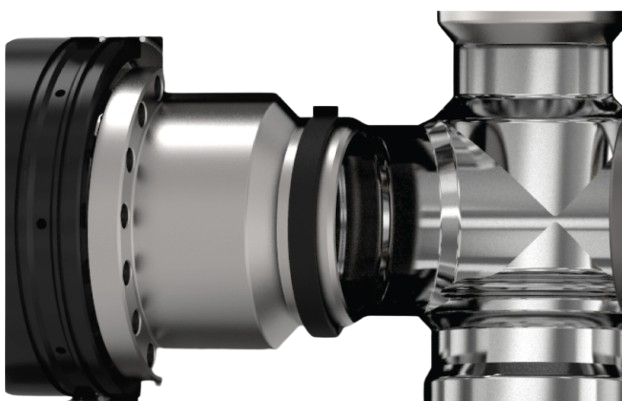
Failure 02
Packing Bore Washouts | Washboarding
Washouts are the #1 cause of fluid end failures today! Kerr Pumps patent-pending Super Seal design has a removable sleeve in the packing area which is a dual sacrificial piece. The sleeve’s internal bore is engineered to save a fluid end from packing washout. The outer surface of the sleeve seals against a seal that is embedded into the fluid end designed to Transfer The Wear from the fluid end to the outside of the sleeve.
Each sleeve is field repairable, providing a windfall of savings for service companies! Beware of using press fit sleeves as they are not only costly, but the need to machine them out is very time consuming! Also, watch out for sleeves that have seals on the face and outer side, because these sleeves just move the failure point from the packing bore to the seal bore.
Every patent-pending Frac One Connect model ships with our Super Seal packing bore sleeves.
Failure 03
Suction Seal Bore Wash/Wear
The cyclic nature of the reciprocating pump is the culprit for causing suction seal bore wash and wear.
As the plunger strokes back and forth, the suction cover breathes. This breathing movement causes the seal to wear out the seal bore in the fluid end. This wear and wash becomes even more accelerated when 100 mesh sand gets into the seal interface. Additionally, if the retainer nut begins to back out during operation, the wash and wear becomes more severe.
Our patent-pending Super Seal® embedded in the fluid end, moves the seal from the suction cover to the fluid end. This enables us to Transfer The Wear™ to the suction cover and away from the fluid end, protecting the fluid end from wash and wear.
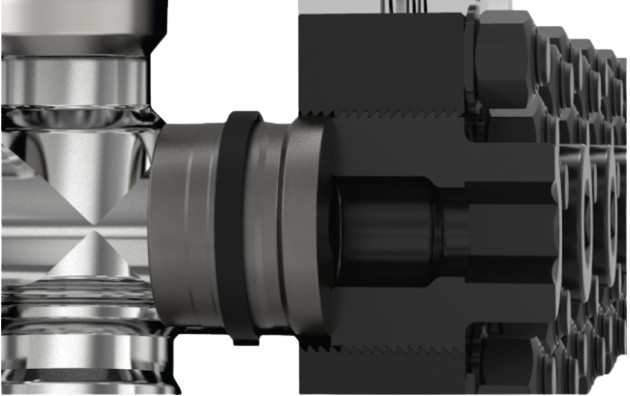
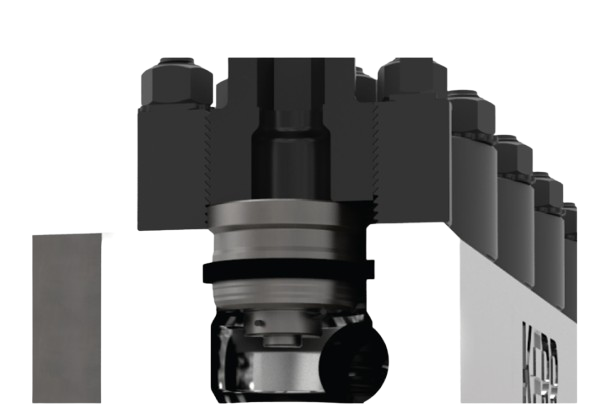
Failure 04
Discharge Seal Bore Wear
The discharge seal bore wears as it rubs against the seal on the discharge plug. During maintenance, when valve seats are pulled to change out parts, the tools used often hit the seal bore damaging the fluid end.
Our patent-pending Super Seal® design creates a groove to house the seal for the discharge bore. Moving the seal groove to the fluid end, enables us to Transfer The Wear™ to the discharge plug, protecting the fluid end.
Failure 05
Valve Seat Deck Washouts/Cracks
The valve seat often cracks inside of the seat flange area. Once the seat cracks, a wash point occurs, washing out the fluid end. Also, changing valve seats are one of the biggest maintenance headaches.
For years, our research and development team has worked with tungsten carbide seats. In that time, we have learned a great deal
• Tungsten carbide performs poorly in tension, but holds up well in compression.
• Tungsten carbide can last up to 10 times the life of normal seats, but it can cost up to 12 times the price of standard seats.
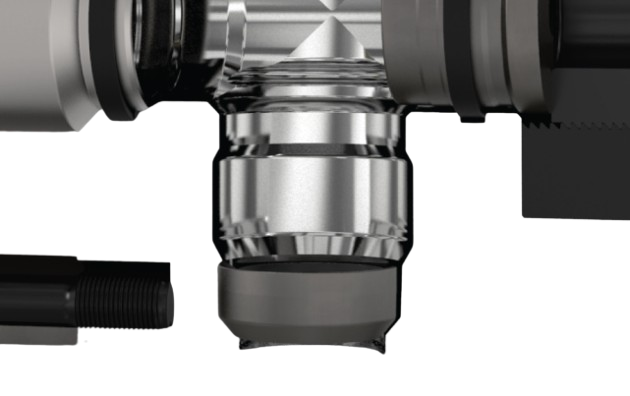
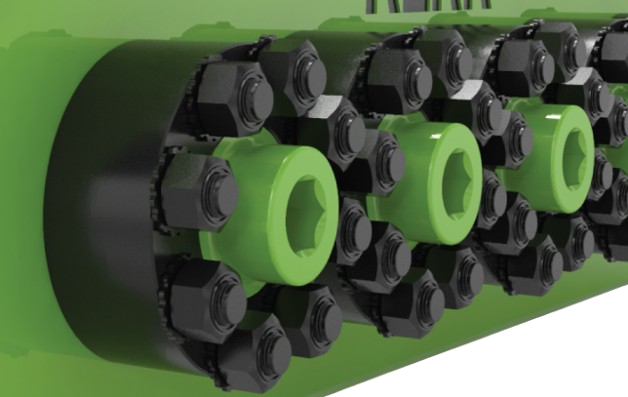
Failure 06
Thread Cracking
The retainer nuts on a 4.5” plunger, pumping at 12,000 PSI, undergoes up to 287,467 lbs of cyclic load. To just equal that pressure load and get it out of cyclic stress, 19,404 lb/ft of torque would need to be applied. All that pressure added to the galling, wear, and tear on the fluid end threads and retainer nuts causes thread cracking.
We developed the patent-pending Frac One bolt on design to combat the problem of thread cracking. By spreading the load to 8 studs per hole, we reduced the load for each stud to 35,934 lbs. And, with each stud torqued to 700 lb/ft cyclic stress was removed.
Failure 07
Flange Failure
Using a flange for the stay rods has never been an optimal solution. Flanges produce a lot of flex in the fluid end and create a great deal of waste in time and material during machining. When flex occurs in a flanged fluid end, it causes the stay rod nuts to lose torque, and can increase the likelihood of fatigue cracking in the intersecting bore (reverse loading). And, on rare occasions, we have even seen cracking happen at the flange.
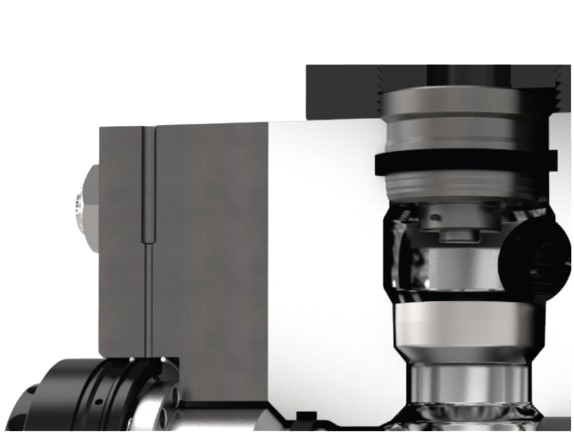
Failure 01
Intersecting Bore Cracking
Intersecting bore cracking was the number one failure for fluid ends until we cracked the code. Kerr Pumps fluid ends are built to frac! Made with Super Stainless II – the strongest and toughest stainless steel ever used in a fluid end – each Kerr Super Stainless fluid end model is engineered with proprietary stress reducing geometries that are optimized to withstand the highest loads in the industry. All of these Transfer the Wear™ design benefits are all available in our all new patent-pending Frac One Connect fluid end!
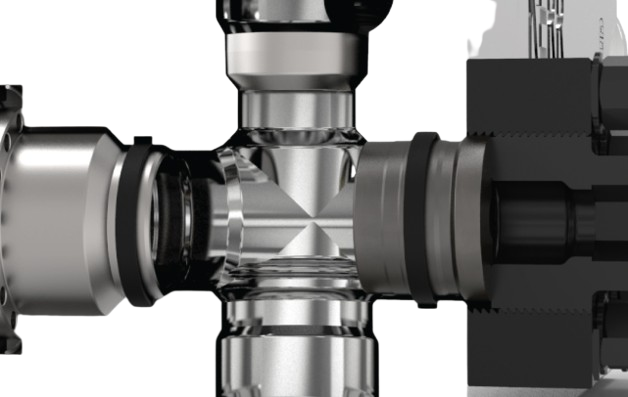
Failure 02
Packing Bore Washouts | Washboarding
Washouts are the #1 cause of fluid end failures today! Kerr Pumps patent-pending Super Seal design has a removable sleeve in the packing area which is a dual sacrificial piece. The sleeve’s internal bore is engineered to save a fluid end from packing washout. The outer surface of the sleeve seals against a seal that is embedded into the fluid end designed to Transfer The Wear from the fluid end to the outside of the sleeve.
Each sleeve is field repairable, providing a windfall of savings for service companies! Beware of using press fit sleeves as they are not only costly, but the need to machine them out is very time consuming! Also, watch out for sleeves that have seals on the face and outer side, because these sleeves just move the failure point from the packing bore to the seal bore.
Every patent-pending Frac One Connect model ships with our Super Seal packing bore sleeves.
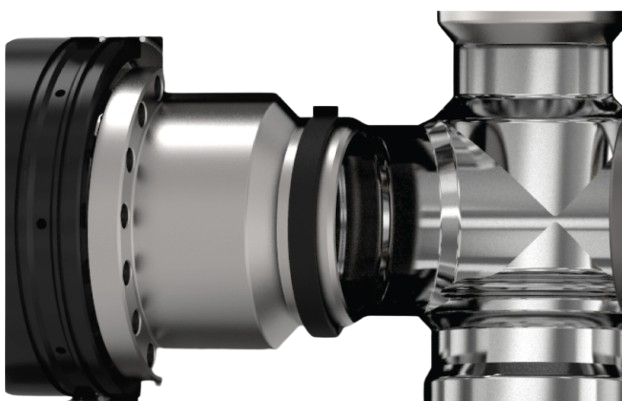
Failure 03
Suction Seal Bore Wash/Wear
The cyclic nature of the reciprocating pump is the culprit for causing suction seal bore wash and wear.
As the plunger strokes back and forth, the suction cover breathes. This breathing movement causes the seal to wear out the seal bore in the fluid end. This wear and wash becomes even more accelerated when 100 mesh sand gets into the seal interface. Additionally, if the retainer nut begins to back out during operation, the wash and wear becomes more severe.
Our patent-pending Super Seal® embedded in the fluid end, moves the seal from the suction cover to the fluid end. This enables us to Transfer The Wear™ to the suction cover and away from the fluid end, protecting the fluid end from wash and wear.
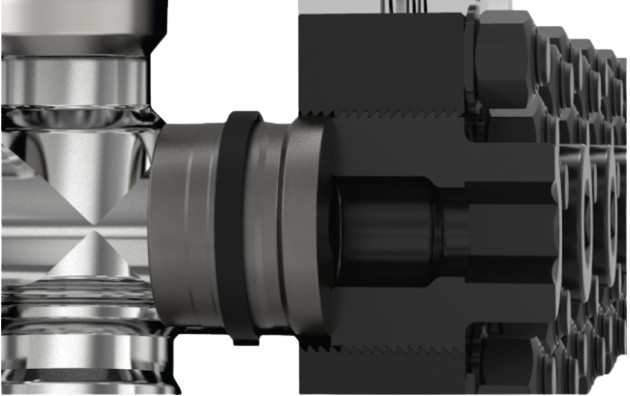
Failure 04
Discharge Seal Bore Wear
The discharge seal bore wears as it rubs against the seal on the discharge plug. During maintenance, when valve seats are pulled to change out parts, the tools used often hit the seal bore damaging the fluid end.
Our patent-pending Super Seal® design creates a groove to house the seal for the discharge bore. Moving the seal groove to the fluid end, enables us to Transfer The Wear™ to the discharge plug, protecting the fluid end.
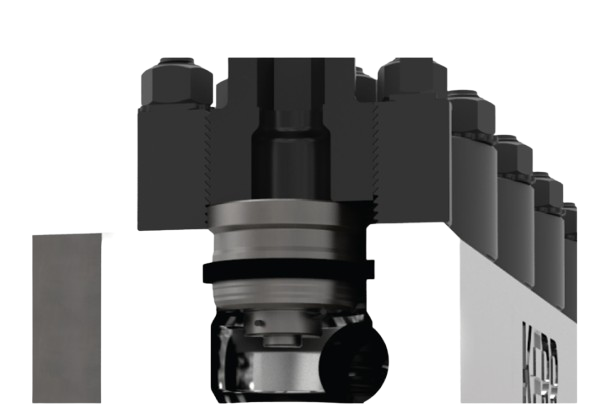
Failure 05
Valve Seat Deck Washouts/Cracks
The valve seat often cracks inside of the seat flange area. Once the seat cracks, a wash point occurs, washing out the fluid end. Also, changing valve seats are one of the biggest maintenance headaches.
For years, our research and development team has worked with tungsten carbide seats. In that time, we have learned a great deal
• Tungsten carbide performs poorly in tension, but holds up well in compression.
• Tungsten carbide can last up to 10 times the life of normal seats, but it can cost up to 12 times the price of standard seats.
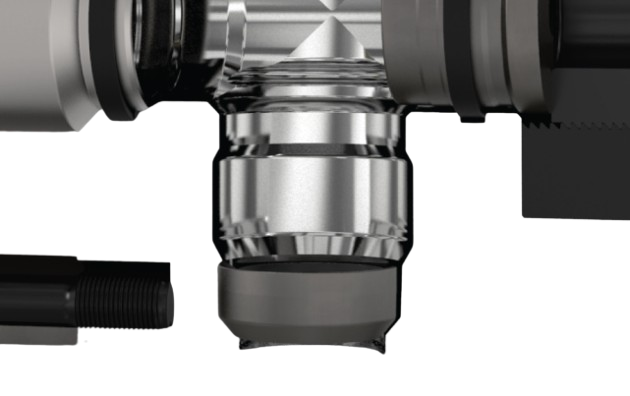
Failure 06
Thread Cracking
The retainer nuts on a 4.5” plunger, pumping at 12,000 PSI, undergoes up to 287,467 lbs of cyclic load. To just equal that pressure load and get it out of cyclic stress, 19,404 lb/ft of torque would need to be applied. All that pressure added to the galling, wear, and tear on the fluid end threads and retainer nuts causes thread cracking.
We developed the patent-pending Frac One bolt on design to combat the problem of thread cracking. By spreading the load to 8 studs per hole, we reduced the load for each stud to 35,934 lbs. And, with each stud torqued to 700 lb/ft cyclic stress was removed.
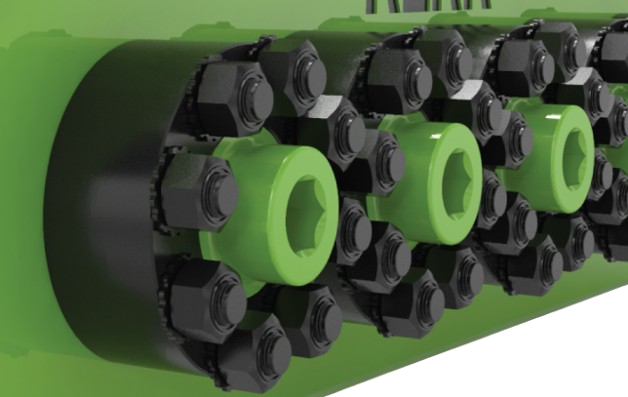
Failure 07
Flange Failure
Using a flange for the stay rods has never been an optimal solution. Flanges produce a lot of flex in the fluid end and create a great deal of waste in time and material during machining. When flex occurs in a flanged fluid end, it causes the stay rod nuts to lose torque, and can increase the likelihood of fatigue cracking in the intersecting bore (reverse loading). And, on rare occasions, we have even seen cracking happen at the flange.
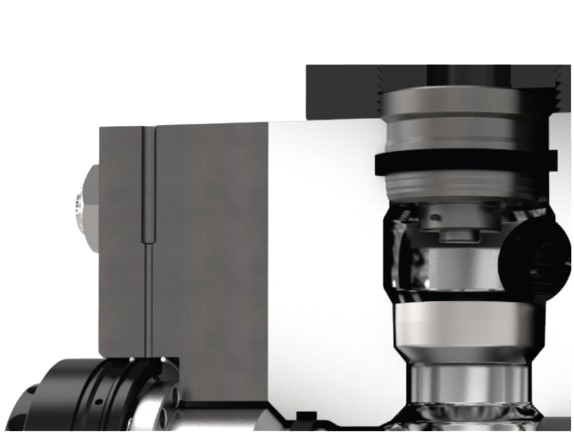
- About industrial Pumps
- Type of Pumps
Industrial Pumps (Plunger and piston Pumps)
Need The Perfect Pumps
Select Your PSI and GPM - Let Kerr Match You with the Ultimate Solution!
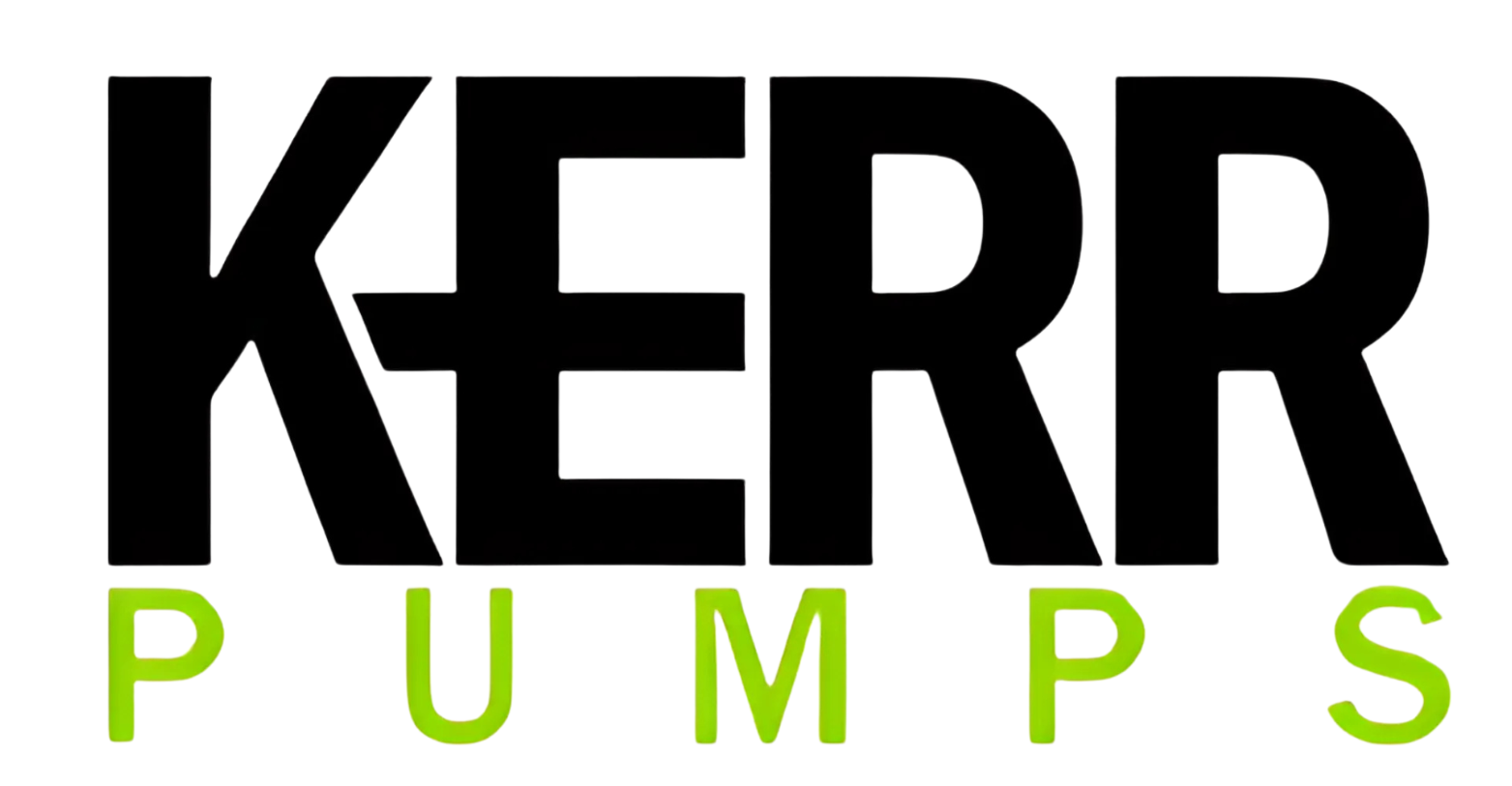
Why Choose Kerr Pumps?
- Decades of Expertise:
Over 75 years of experience in engineering dependable pumps. - Innovative Designs:
Advanced technology for high performance and reliability. - Custom Options:
Specialty metallurgy available for unique industrial requirements. - American-Made Quality:
All products are designed, manufactured, and tested in the USA.
Plunger & Piston Pumps
- Over 100 Standard Models
- Power Range: 5 – 625 BHP
- Flow Rate: Up to 600 GPM (Gallons Per Minute)
- Volume: Up to 21,000 BPD (Barrels Per Day)
Applications
Oil & Gas Industry
- Horizontal Directional Drilling (HDD)
- Sand Fracing
- Oil Pipeline Transfer
- Well Kill Trucks
Municipal and Public Services
- Fire Control Services
- Public Transport
- Municipal Services
Industrial Applications
- Mining
- Chemical Industry
- Hydraulic Power
- High-Pressure Water Jetting
Specialized Fields
- Descaling Steel
- Reverse Osmosis
- Food & Beverage Industry
- Nuclear Power Plants
Construction & Agriculture
- Cement Slurry
- Construction Industry
- Agriculture
Others
- Hydrostatic Testing
- Car Wash Systems (Self-Serve, Automatic, Touchless)
- Military Service
- Ship Building
Type of Pumps
T - Series
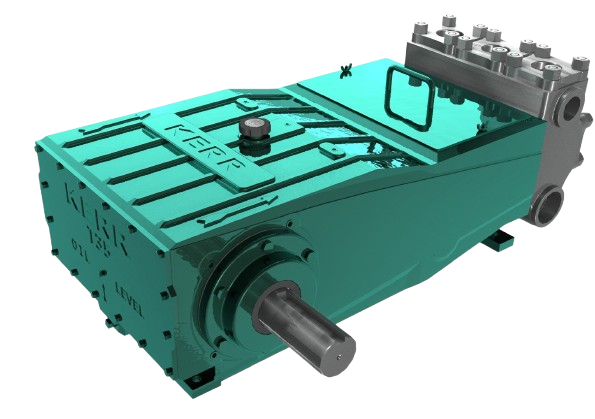
T25M
T30MM
T25H
T30MH
T30M
T30XP
T30H
T35M
T35XP
T35H
T40M
T40XP
T40H
T40M
T50M
T50XP
T50H
T60WS
Q - Series
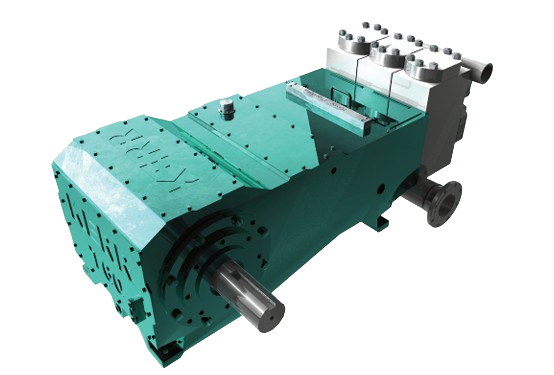
K - Series
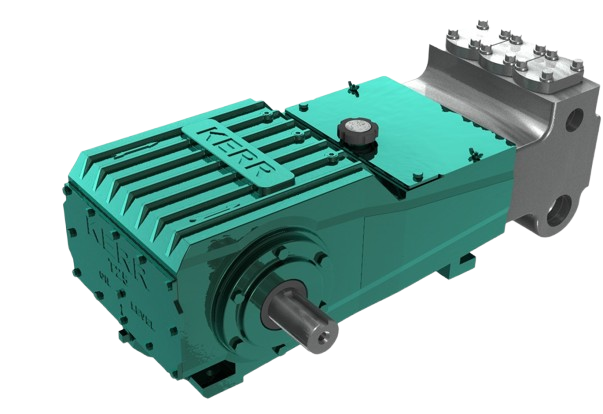
KD-1250BC
KJ-2250BC
KZ-3150PT
KZ-3150
KM-3250BC
KM-3250BCB
KP-3300BC
KP-3300HP
KP-3300BCB
KT-3350
KT-3350XP
KT-3350HP
KT-3350BCB
KT-3400
KT-3400XP
KT-3400HP
KT-3400BCB
KA-3500
KA-3500HP
KA-3500BCB
Kerr Original Parts
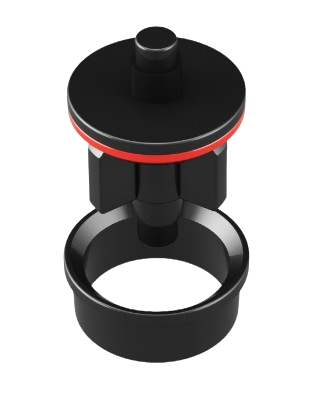
Plungers
We continue to develop the most advanced coating technologies that cover a wide range of applications. We stock four premier plungers that include: tungsten carbide, ceramic, Kerramic and Black Gold. Our tungsten carbide plunger lasts twice as long as the nickel alloy that exhausts the marketplace.
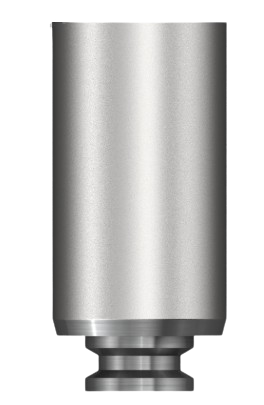
Valves and Seats
Kerr Pumps manufacturers a wide variety of high quality valves and seats. We offer plenty of configurations and materials to choose from such as our more popular salt bath nitrided 17-4 stainless steel. We also keep in stock a full line of Well Service inserted valves and o-ringed seats.
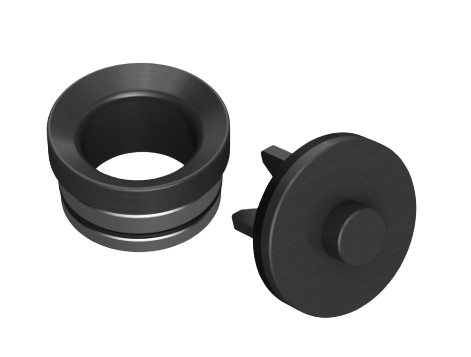
Piston Cup Assembly
Our engineers have developed piston assemblies with precision molded replaceable piston cups, molded in fabric reinforced nitrile rubber. Coupled with a 300 series stainless steel piston body, this assembly ensures optimum corrosion and abrasion resistance, regardless of liner material.
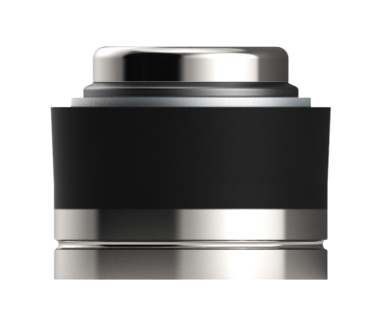
Stuffing Boxes
We manufacture replacement stuffing boxes in a variety of styles, sizes and materials for a broad range of packing arrangements and elastomers. The necessary precision in each box enables a perfect interface for maximum packing life even in the most demanding temperature and pressure conditions.
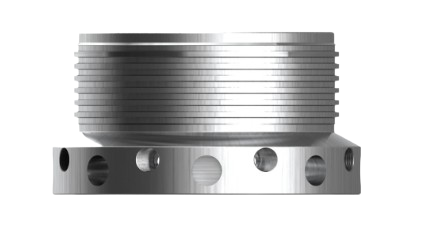
Connecting Rods
The entire Kerr Pumps product line utilizes high strength cast ductile iron, maintaining stable housings for precision fit wrist pin bushings and crankshaft inserts. Each connecting rod is made from U.S. foundries and is machined on one of our precision CNC horizontal machining centers.
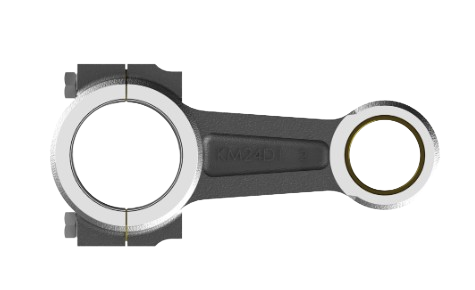
Pony Rod Glands
All of our pony rod glands are machined in-house on one of our many CNC lathes. The level of precision and finish in each gland gives an incredible repeatability from part to part. This consistency extends the life of each seal and pony rod which keeps you pumping longer in the field.
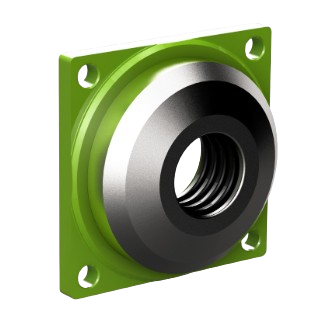
And Many More!
We believe that making incredible pumps is just part of the game. Our main focus is taking care of our customers. That is why we stock a full line of pump replacement parts. We do our absolute best in meeting customer demands and continue to strive to be the most responsive pump company.
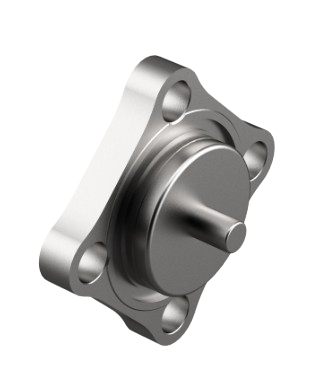
Plungers
We continue to develop the most advanced coating technologies that cover a wide range of applications. We stock four premier plungers that include: tungsten carbide, ceramic, Kerramic and Black Gold. Our tungsten carbide plunger lasts twice as long as the nickel alloy that exhausts the marketplace.
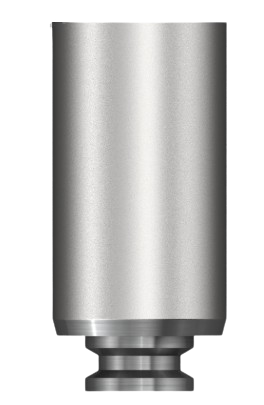
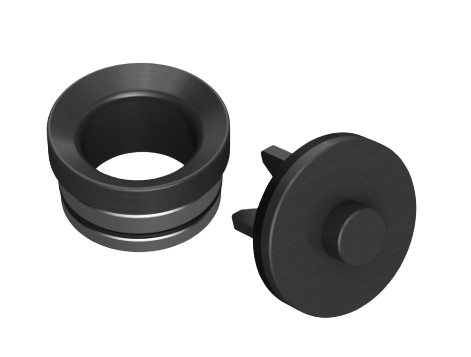
Valves and Seats
Kerr Pumps manufacturers a wide variety of high quality valves and seats. We offer plenty of configurations and materials to choose from such as our more popular salt bath nitrided 17-4 stainless steel. We also keep in stock a full line of Well Service inserted valves and o-ringed seats.
Piston Cup Assembly
Our engineers have developed piston assemblies with precision molded replaceable piston cups, molded in fabric reinforced nitrile rubber. Coupled with a 300 series stainless steel piston body, this assembly ensures optimum corrosion and abrasion resistance, regardless of liner material.
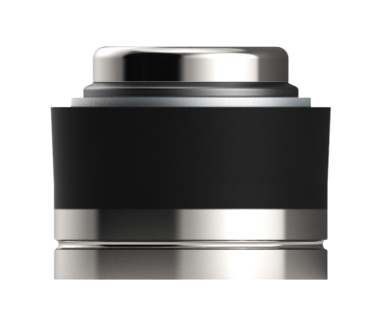
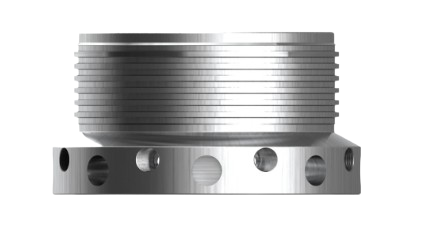
Stuffing Boxes
We manufacture replacement stuffing boxes in a variety of styles, sizes and materials for a broad range of packing arrangements and elastomers. The necessary precision in each box enables a perfect interface for maximum packing life even in the most demanding temperature and pressure conditions.
Connecting Rods
The entire Kerr Pumps product line utilizes high strength cast ductile iron, maintaining stable housings for precision fit wrist pin bushings and crankshaft inserts. Each connecting rod is made from U.S. foundries and is machined on one of our precision CNC horizontal machining centers.
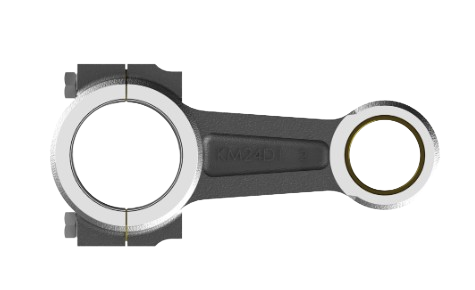
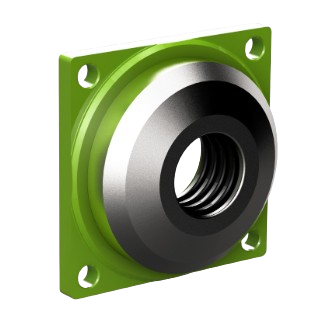
Pony Rod Glands
All of our pony rod glands are machined in-house on one of our many CNC lathes. The level of precision and finish in each gland gives an incredible repeatability from part to part. This consistency extends the life of each seal and pony rod which keeps you pumping longer in the field.
And Many More!
We believe that making incredible pumps is just part of the game. Our main focus is taking care of our customers. That is why we stock a full line of pump replacement parts. We do our absolute best in meeting customer demands and continue to strive to be the most responsive pump company.
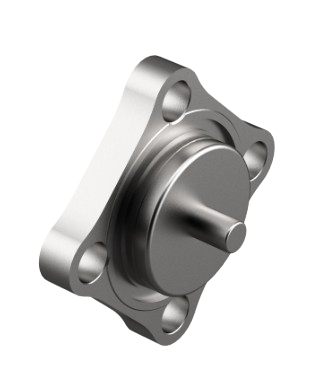
Type of Pumps
T - Series
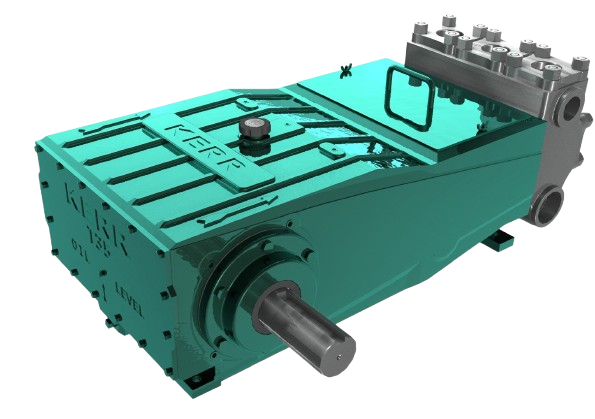
T25M
T30MM
T25H
T30MH
T30M
T30XP
T30H
T35M
T35XP
T35H
T40M
T40XP
T40H
T40M
T50M
T50XP
T50H
T60WS
Q - Series
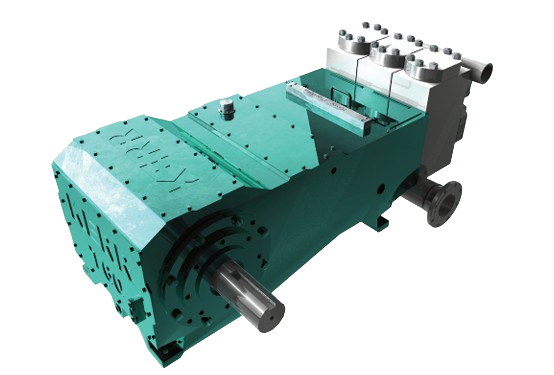
K - Series
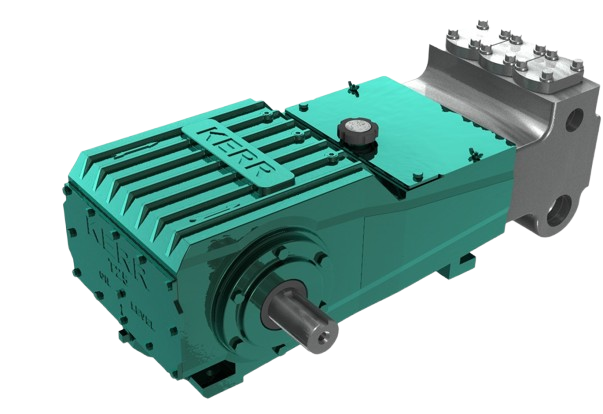